Battery Management Systems
Our cutting-edge BMS HIL test solution is designed to seamlessly emulate battery cell communication using advanced cell virtualization technology. Through strategic collaborations with leading battery cell emulator partners and unparalleled BMS modeling expertise, our solution enables the seamless integration of emerging technologies while ensuring reliable, high-performance BMS testing equipment. With over 30 global deployments, we deliver a proven and future-ready approach to battery management system validation.
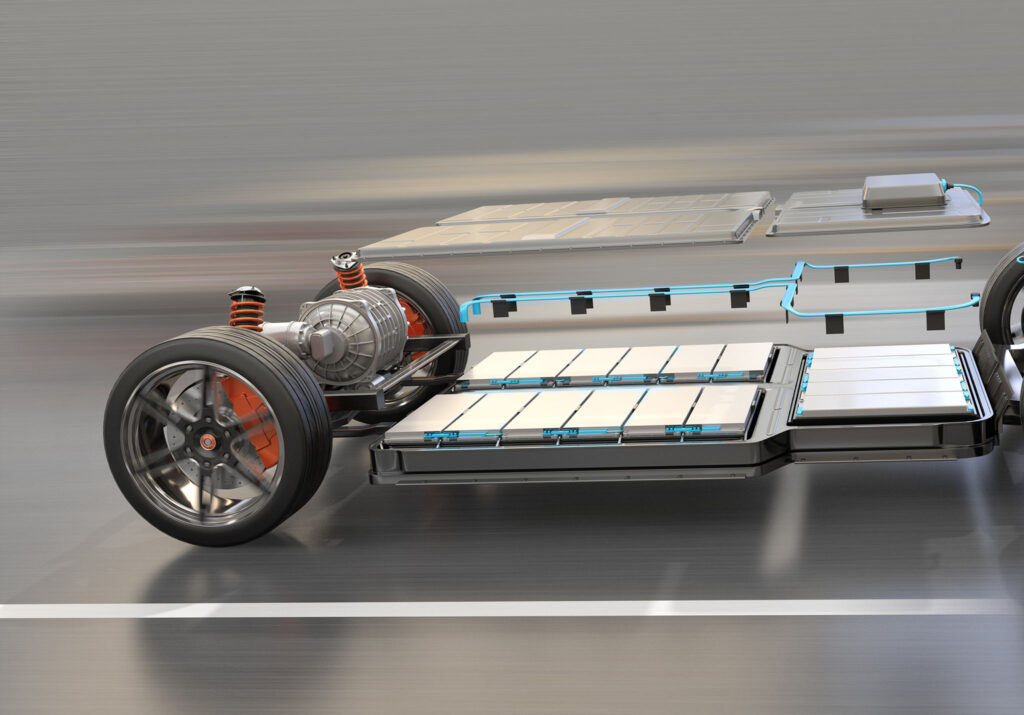
They trust us
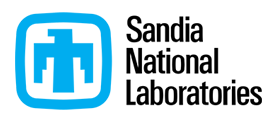
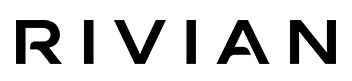
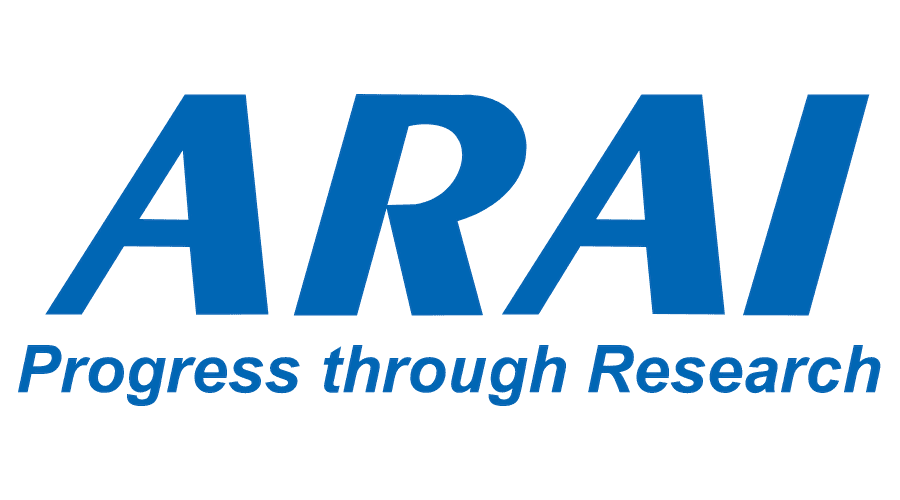
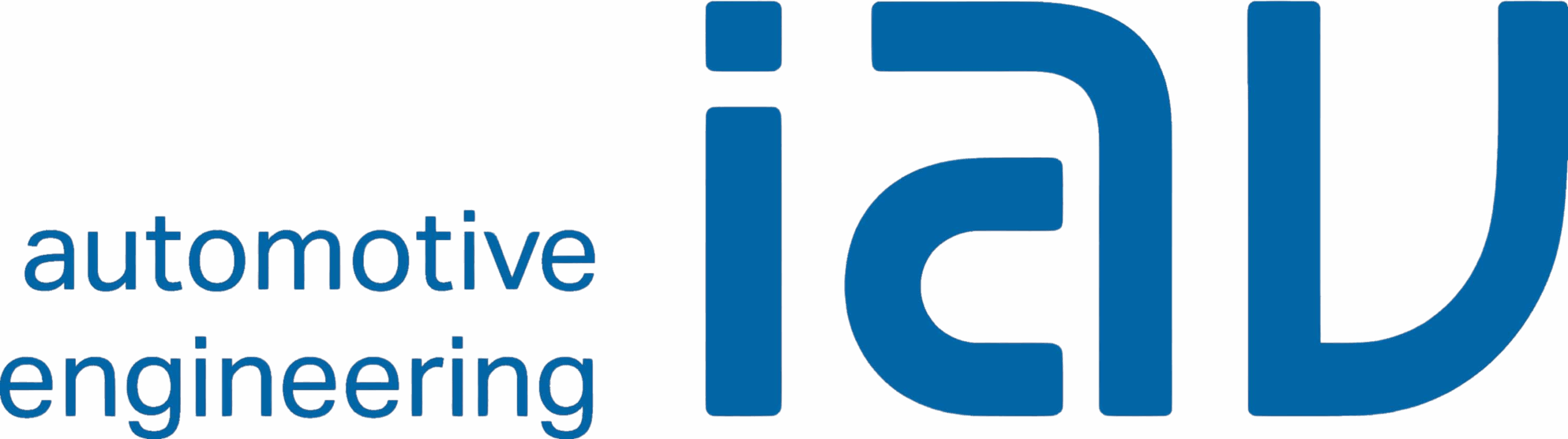
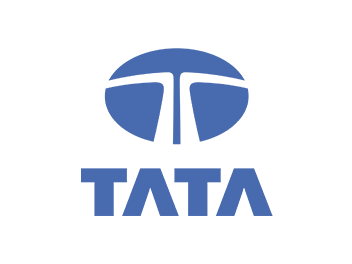
Solution
Validate your BMS with an OPAL-RT system
Our battery management system testing system offers dual cell emulation methods. You can opt for a high-precision battery cell emulator with active voltage sensing and comprehensive fault simulation or choose our proprietary CMDE technology via SPI, which streamlines communication while delivering exceptional accuracy and high-precision current measurement.
Battery cell simulator
Each comemso® BCS unit provides 12 cells and combines high-precision battery cell emulation with active sense adjustment on each voltage. Each cell includes fault simulation for generating short circuits, cable breakage and reverse polarity, as well as a high precision current measurement system.
Real-time simulator
All our BMS simulators support MATLAB/SIMULINK™, where battery, high-fidelity power electronics, motor, and virtual control unit models can all be simulated deterministically. Increase your test coverage by virtualizing your cell monitoring devices using our Cell Monitoring Device Emulation add-on.
Engineering
Extend your BMS HIL testbed functionalities with our engineering services. From extra protection, shunt emulation, break-out boxes, and current and voltage sensing to complete vehicle control or autonomous systems integration.
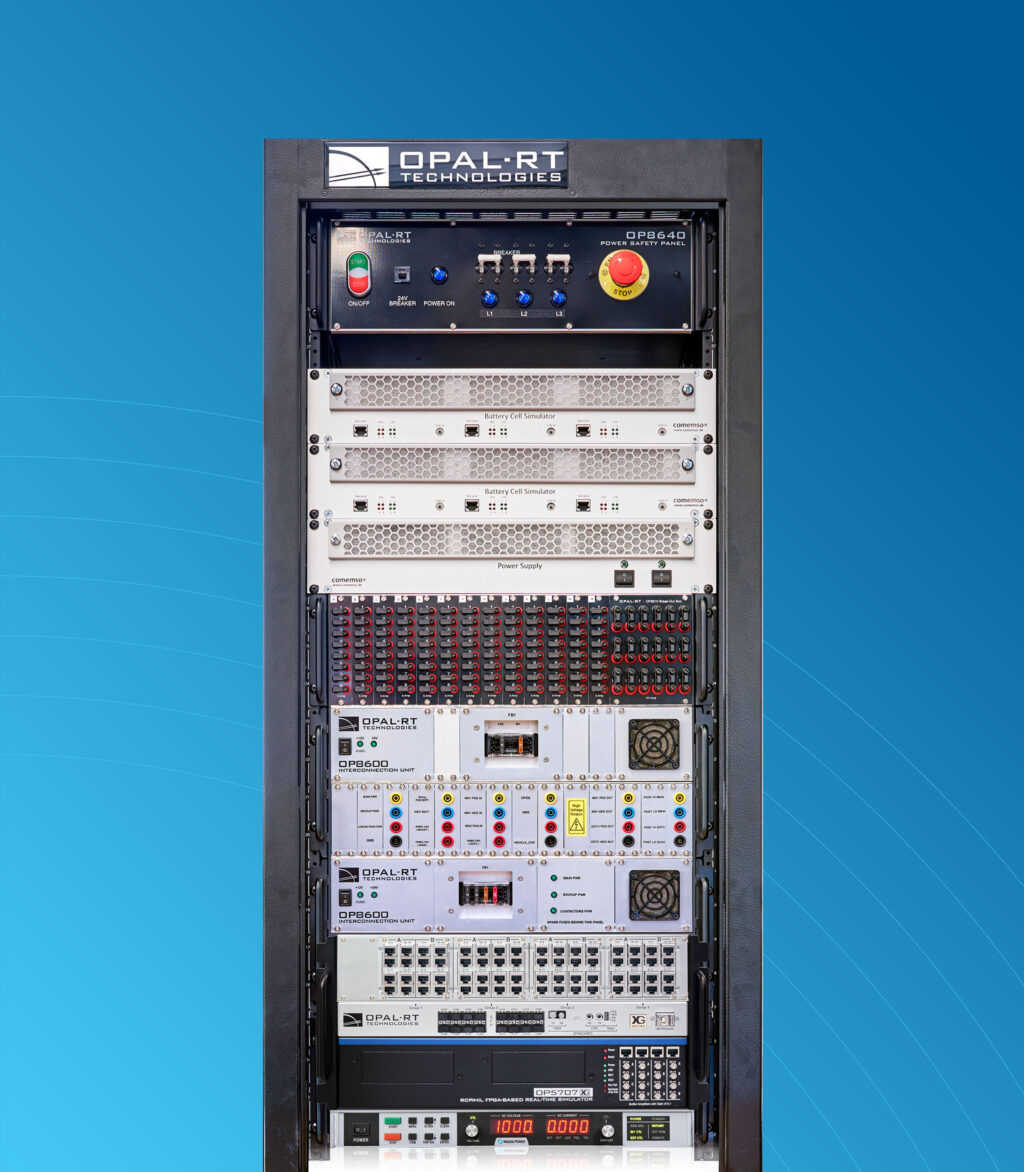
Demo
Testing multiple ECUs in one test bench
In this demo, learn how to implement BMS modelling and simulation for power electronics on FPGA and prepare a HIL system allowing for high performance paired with flexibility for rapid test changes.
This demonstration features power electronics and electric motors simulated on an NI FPGA using our Power Electronics Add-On for NI VeriStand used to validate a Pi-Innovo ECU, as well as MATLAB/SIMULINK™ battery models imported into VeriStand and CAN used to communicate with battery cell simulators to validate an ORION BMS. Prototype and validate your control algorithms throughout your design process using only one test bench.
Software
Cell Monitoring Device Emulation (CMDE)
We developed our own emulation of BMS cell monitoring devices from major brands such as Analog Devices, Inc. (ADI). With our CMDE add-on for NI VeriStand, quickly test and validate your BMS control by emulating the battery cells and BMS chipset register commands using digital communication while maintaining the integrity of the daisy-chain. As a plus, the CMDE add-on also allows for physical comemso® cells to be connected to physical BMS chipsets, while the remaining daisy-chain is kept virtual.
The CMDE tool reduces cost and complexity and extends testing coverage, allowing users to validate their BMS simulation software and meet demanding deadlines.
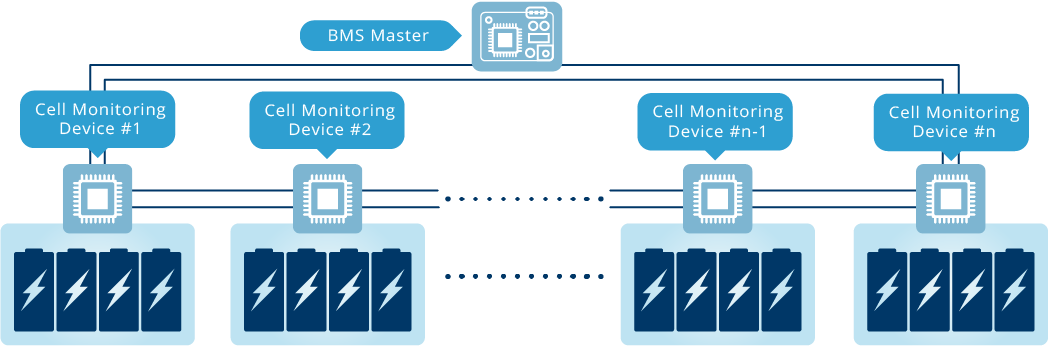
Webinar
Innovations in Battery Management Systems validation
Join us as we discuss innovations in BMS validation, from electric vehicle to grid storage applications, and how we can ensure that your battery management systems test systems are on the leading edge of innovation. In this webinar series, learn both the challenges and proven solutions in validating your battery management systems with brilliant experts in the field.
FAQ
Find the answers to your questions
I’m developing a BMS, how do I know what testing technology I need?
We suggest aiming for as much test coverage as possible with our hybrid solutions, which combine physical BCS’ with virtualization technology to emulate the cell monitoring devices, which also optimizes safety, cost, and hardware footprint. We are happy to work with you and our network of experts to spec a system that meets your needs best.
What communication protocols do you support?
Consult our comprehensive list of supported protocols here.
How does OPAL-RT’s BMS simulator support effective battery management system testing?
Our BMS simulator is designed to bridge the gap between design and practical implementation. By integrating high-fidelity real-time simulation with hardware-in-the-loop (HIL) techniques, it enables comprehensive battery management system testing. This robust platform supports BMS HIL testing, allowing engineers to emulate actual battery cell responses and system behaviors in a controlled environment. As a result, the test process becomes more repeatable and efficient, ultimately leading to safer and more reliable battery systems.
What types of BMS testing equipment and test software does OPAL-RT provide?
We offer a broad suite of tools that includes state-of-the-art BMS testing equipment designed to emulate individual battery cells and aggregate battery packs. Alongside this hardware, their platforms support specialized BMS test software, ensuring that all aspects of BMS testing—from component-level assessments to system-wide verifications—are thoroughly evaluated. This integrated approach to BMS testing and BMS simulation ensures that every detail is captured, helping engineers refine their designs before moving toward live demonstrations or deployment.
What role does BMS simulation software play in developing modern battery systems?
BMS simulation software is central to the iterative design and validation process of modern battery systems. It allows developers to run complex simulations that incorporate electrical, thermal, and chemical behaviors in batteries. By leveraging advanced BMS simulation software, engineers can perform detailed analyses, ranging from nominal operating conditions to extreme edge cases, ensuring the battery management system performs reliably under all conditions. This proactive approach not only enhances overall system safety but also reduces time to market by streamlining the development workflow.
How does BMS HIL testing accelerate development and improve reliability?
BMS HIL testing combines the precision of real-time simulation with actual hardware components, creating a robust environment in which a battery management system can be rigorously evaluated. This method allows for immediate feedback on system performance during simulated stress conditions, faults, or rapid charge/discharge cycles. By incorporating BMS HIL testing into the design process, engineers can quickly iterate and optimize their systems, drastically reducing development cycles and minimizing risks before full-scale production. This integration of simulation and physical testing ultimately leads to a more reliable and efficient battery management solution.