Your testing platform for automotive simulation
For over 25 years, OPAL-RT has worked with major OEM, tier-ones and emerging players in the testing and development of 21st-century automotive technologies. From specialized farm machinery to the mass-production of hybrid vehicles and luxury automobiles, OPAL-RT’s leadership position in HIL testing for automotive simulation is recognized around the world.
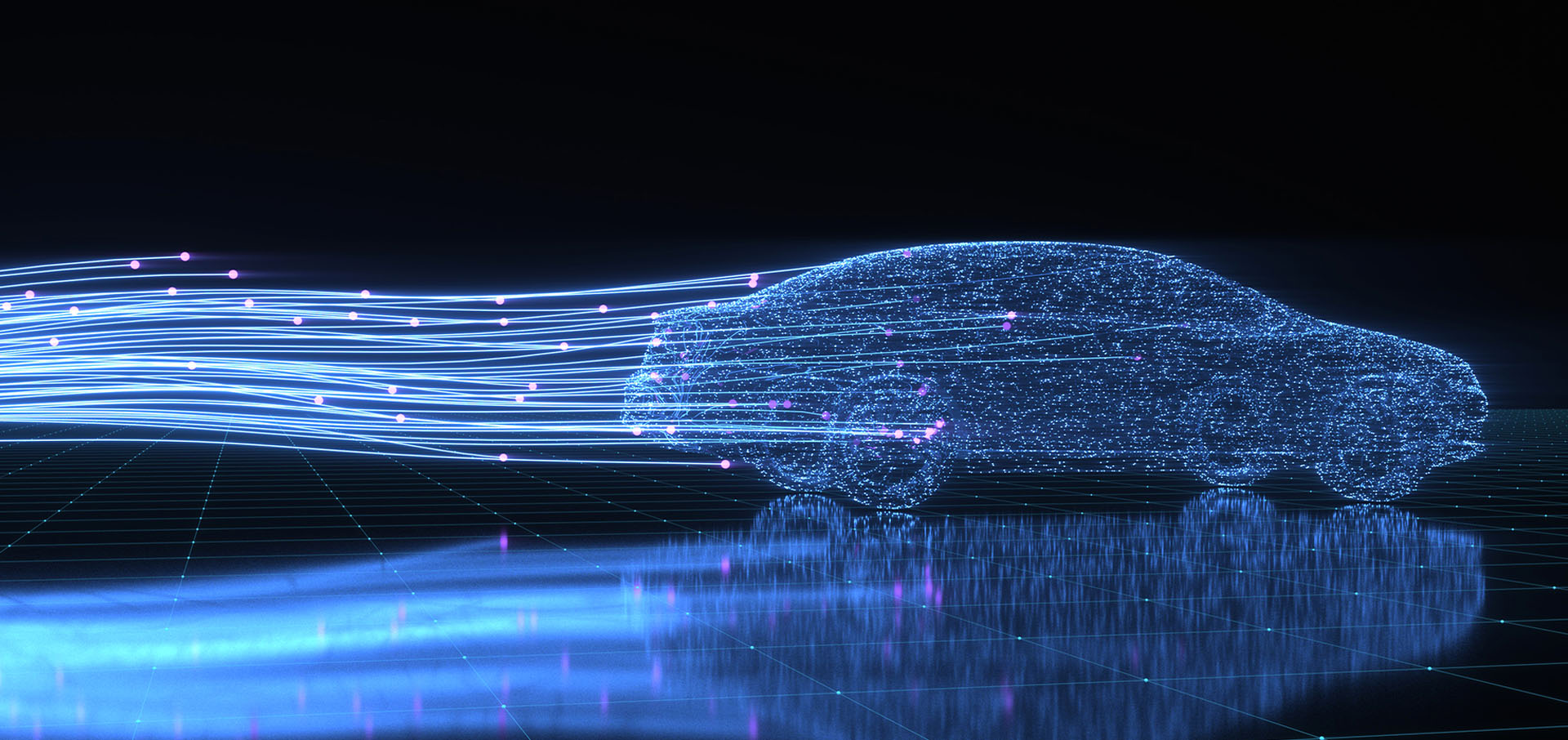
They trust us
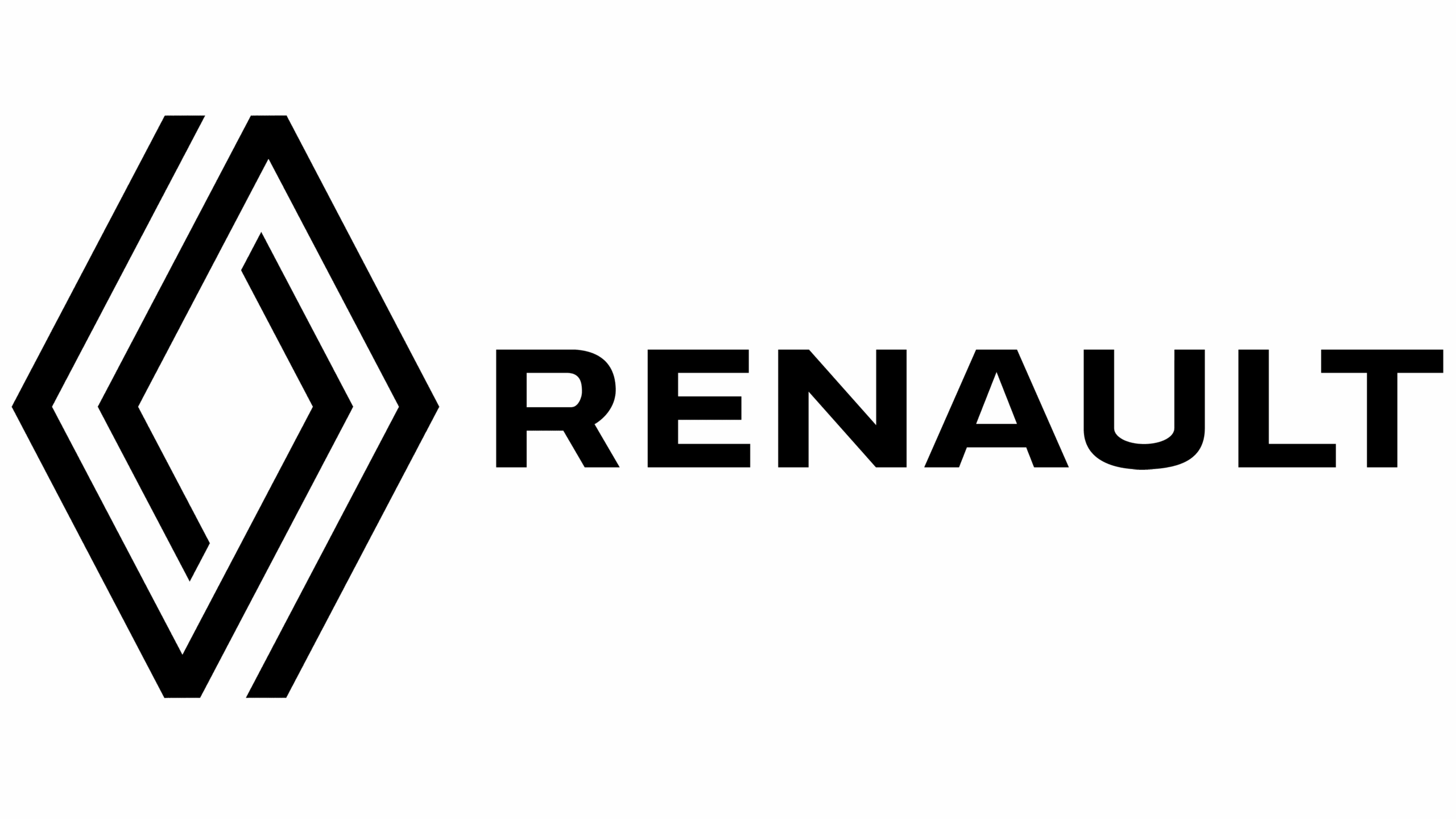
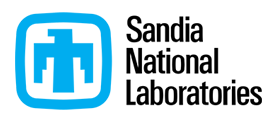
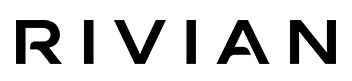
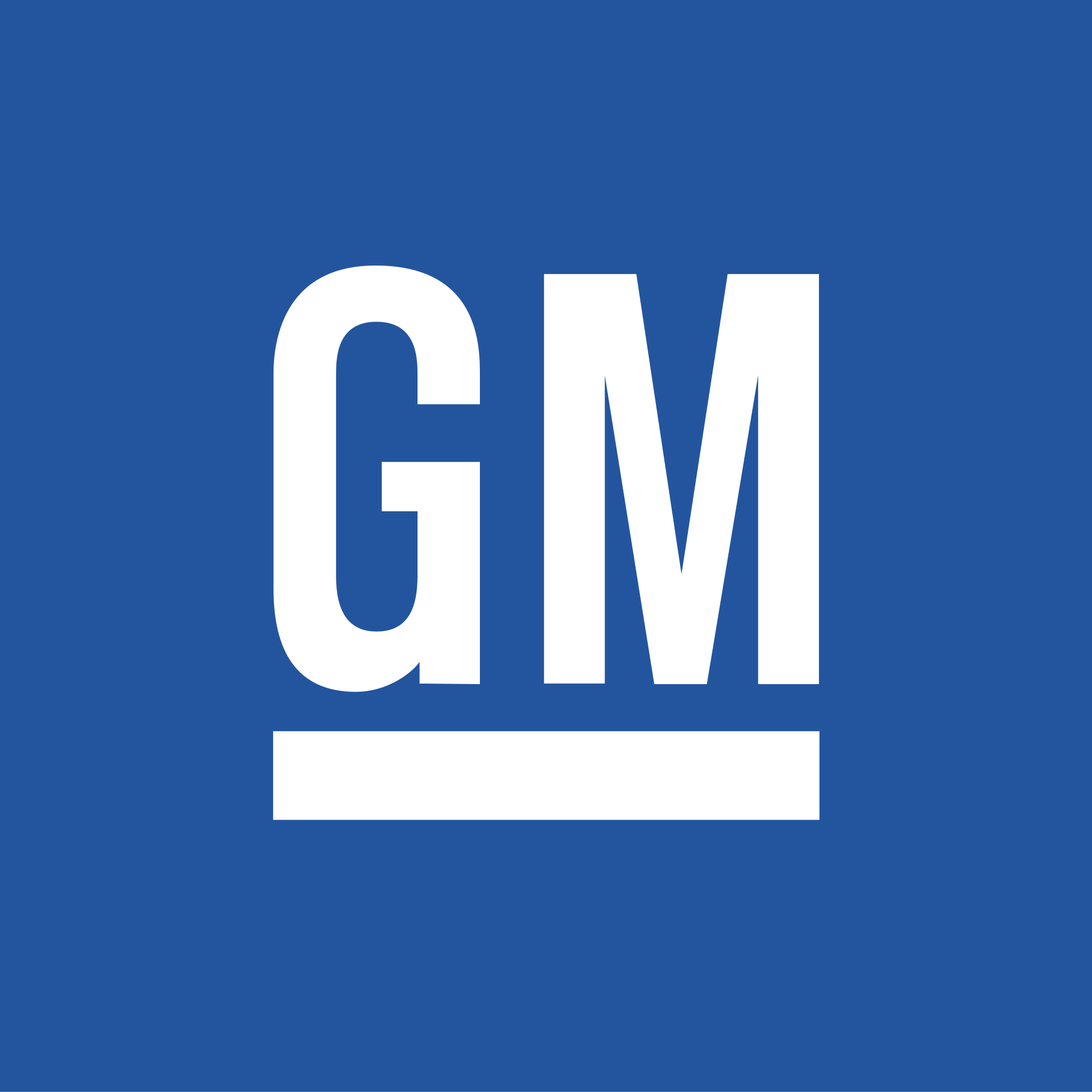
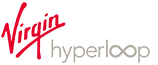
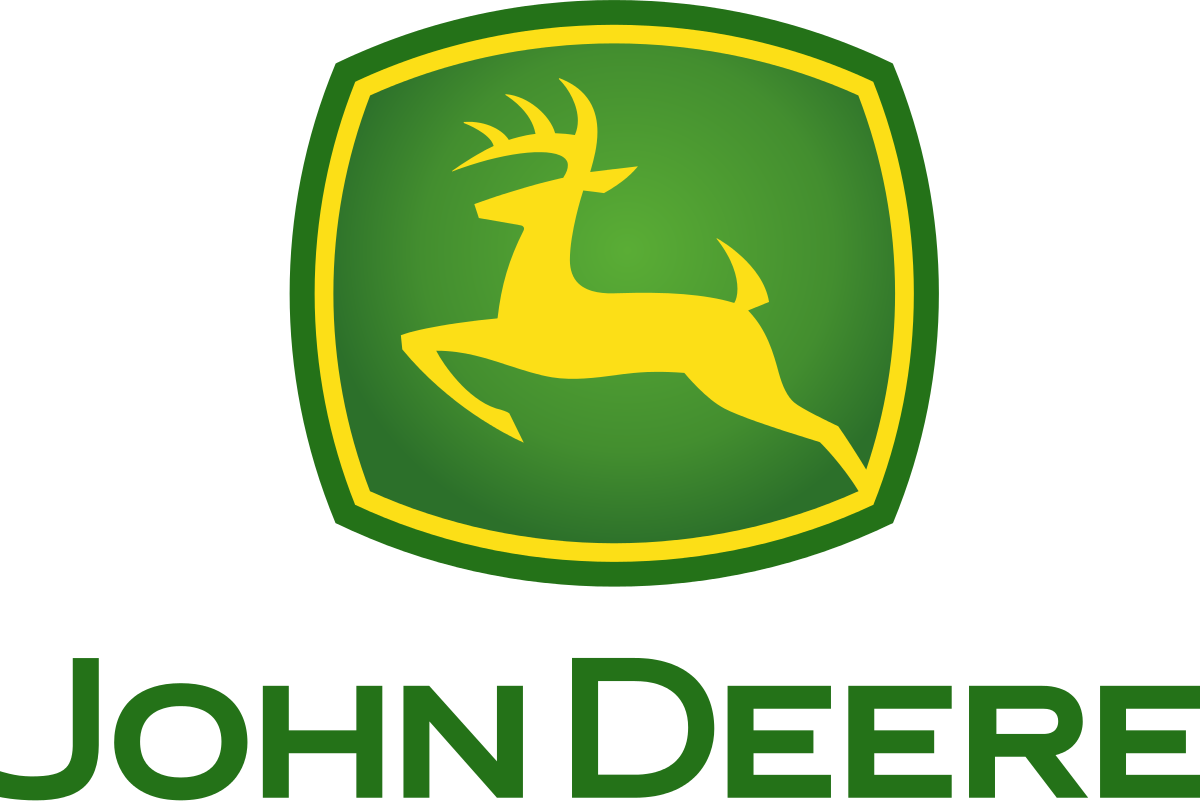
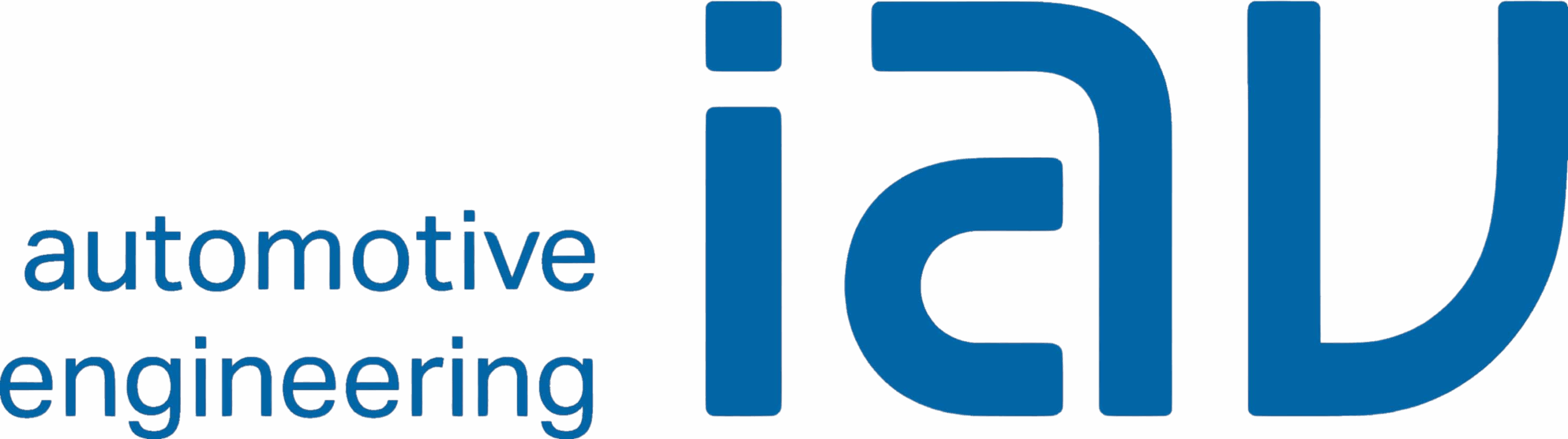
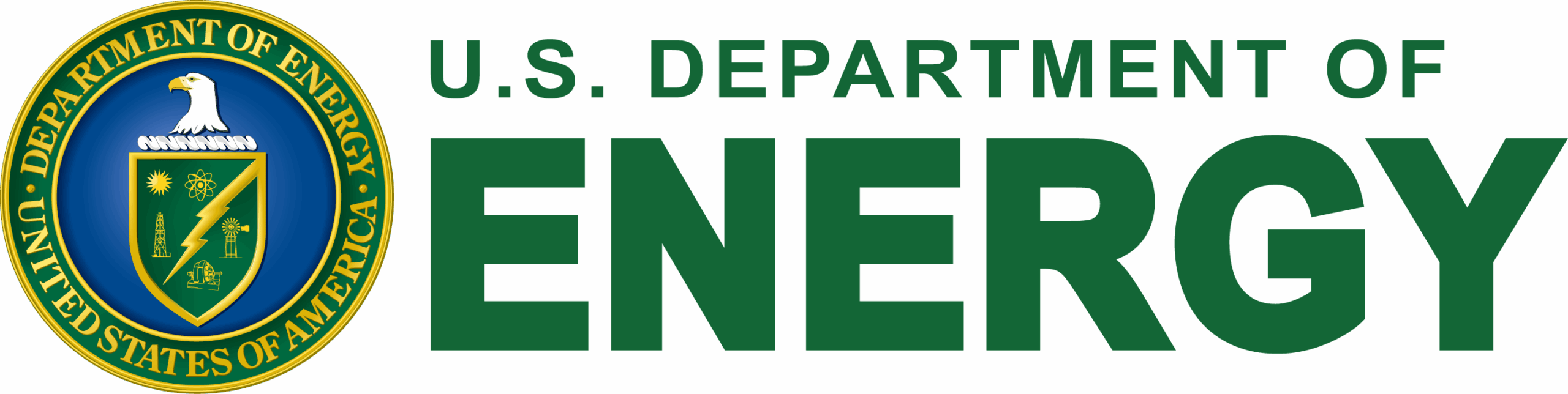
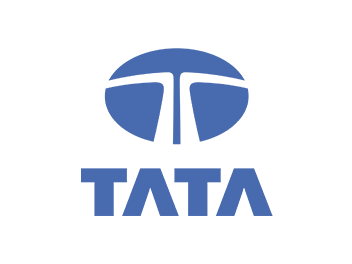
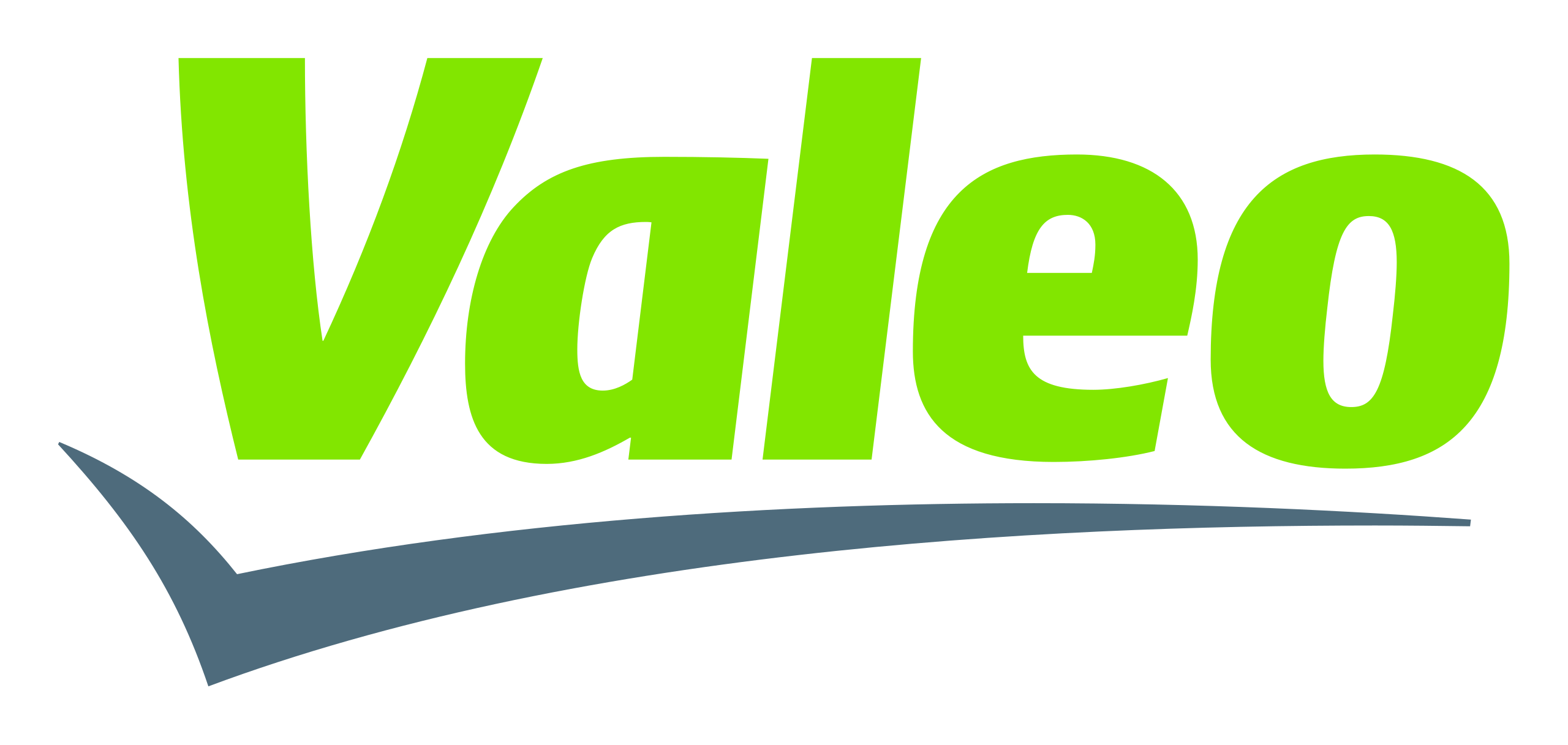
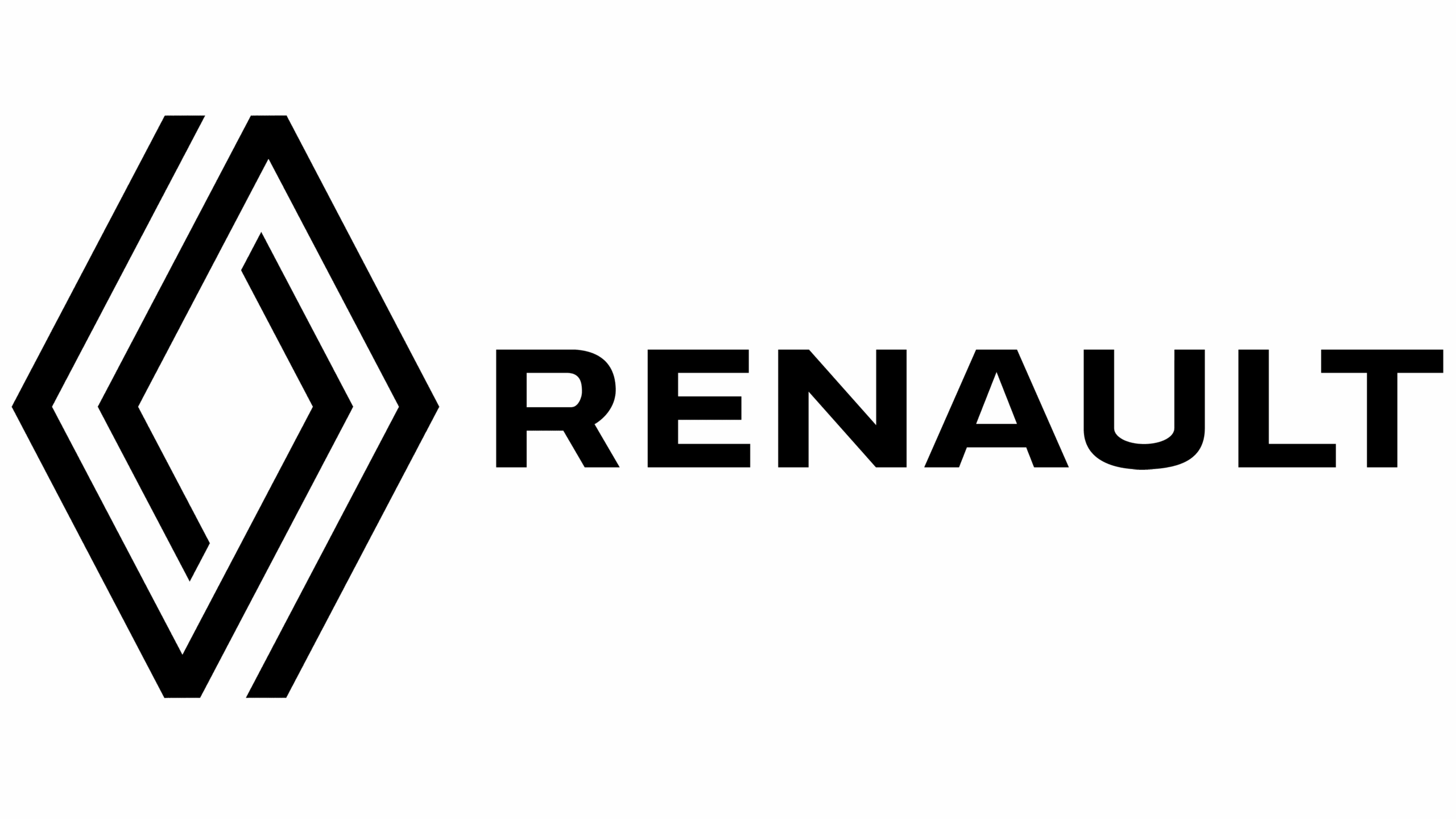
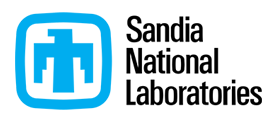
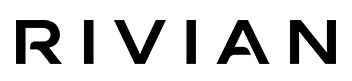
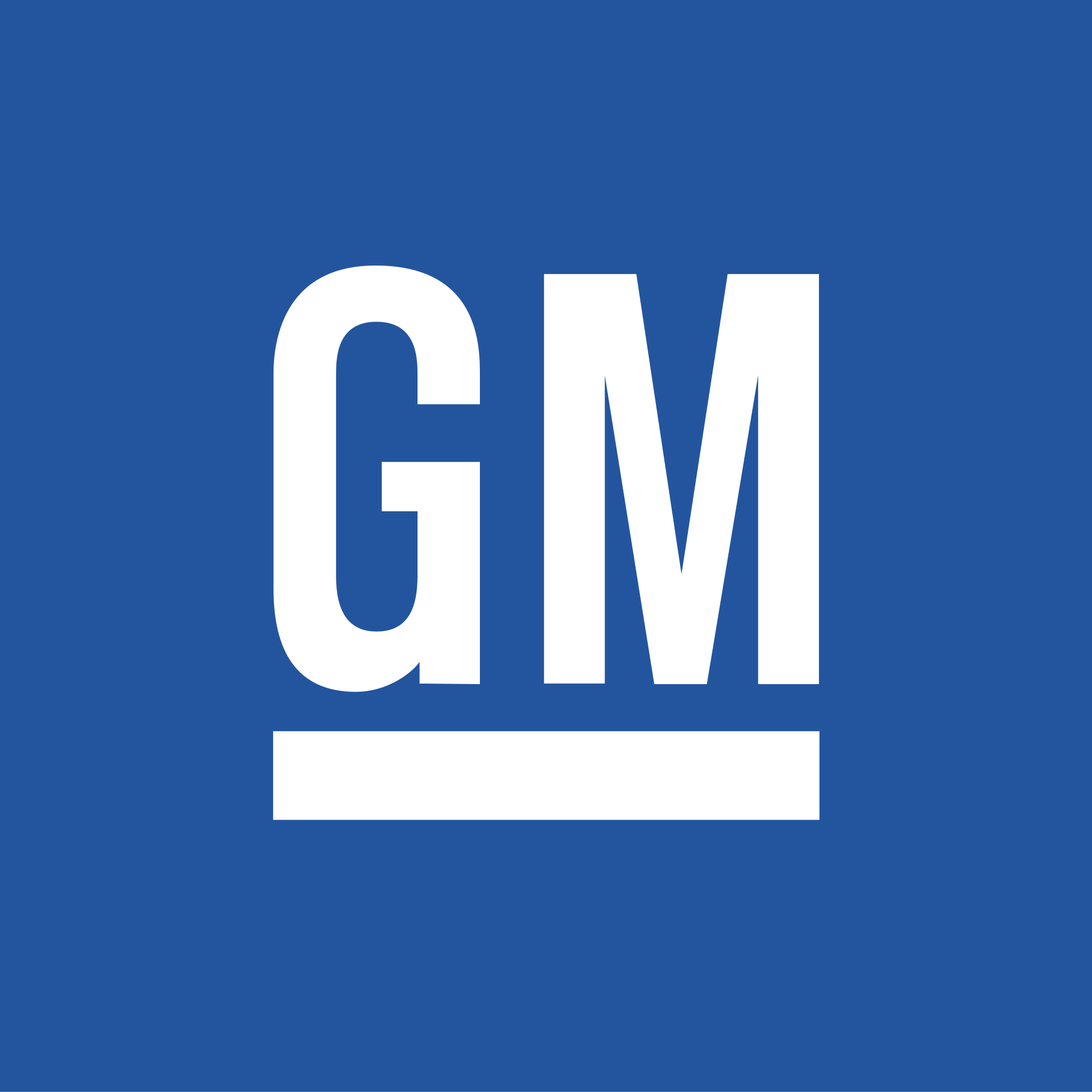
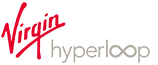
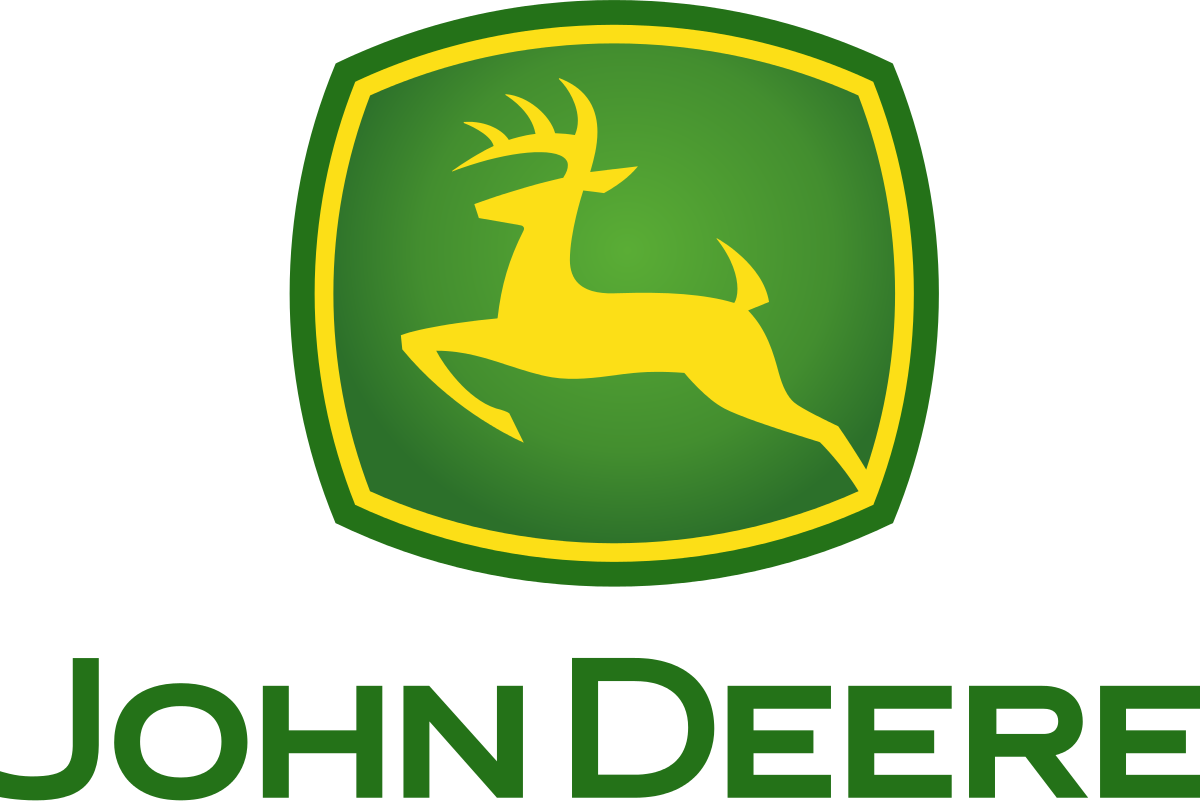
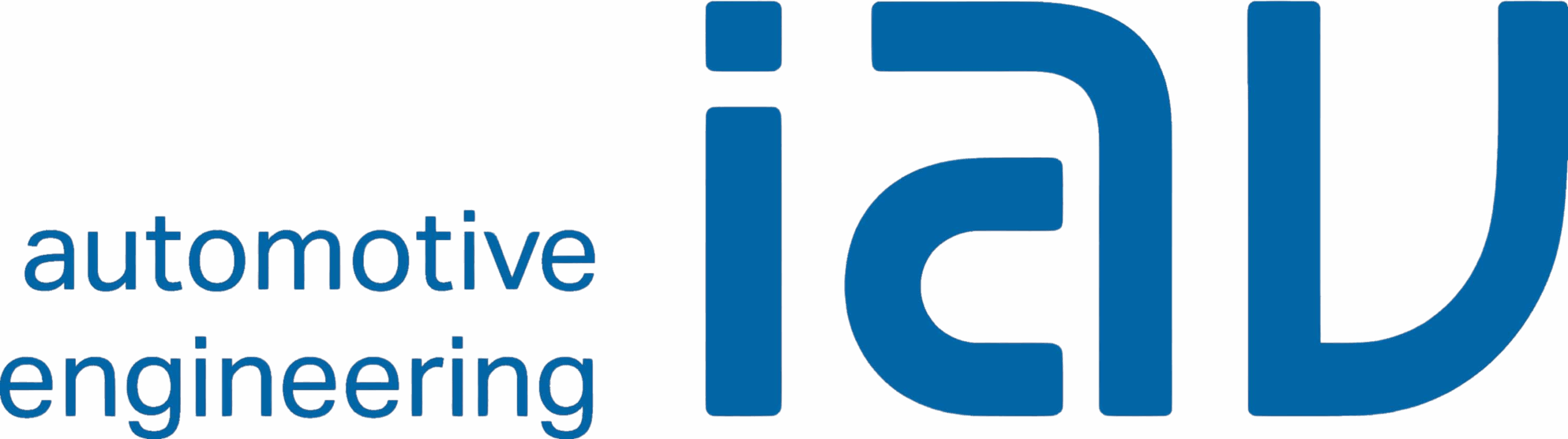
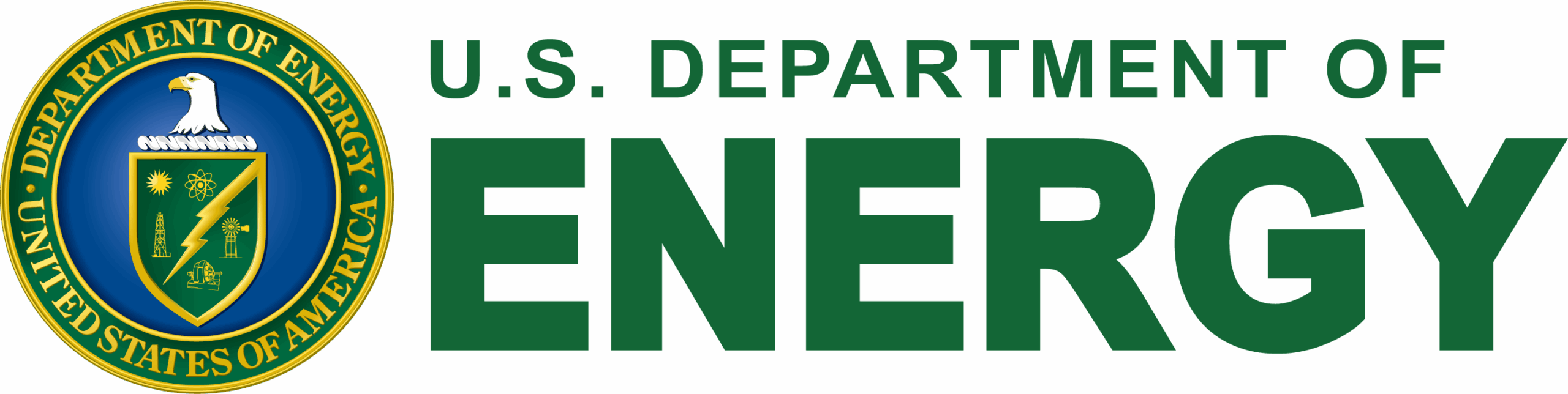
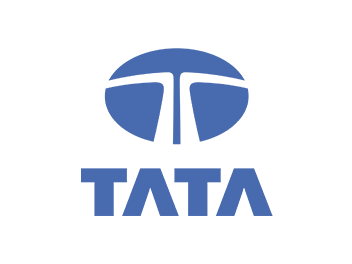
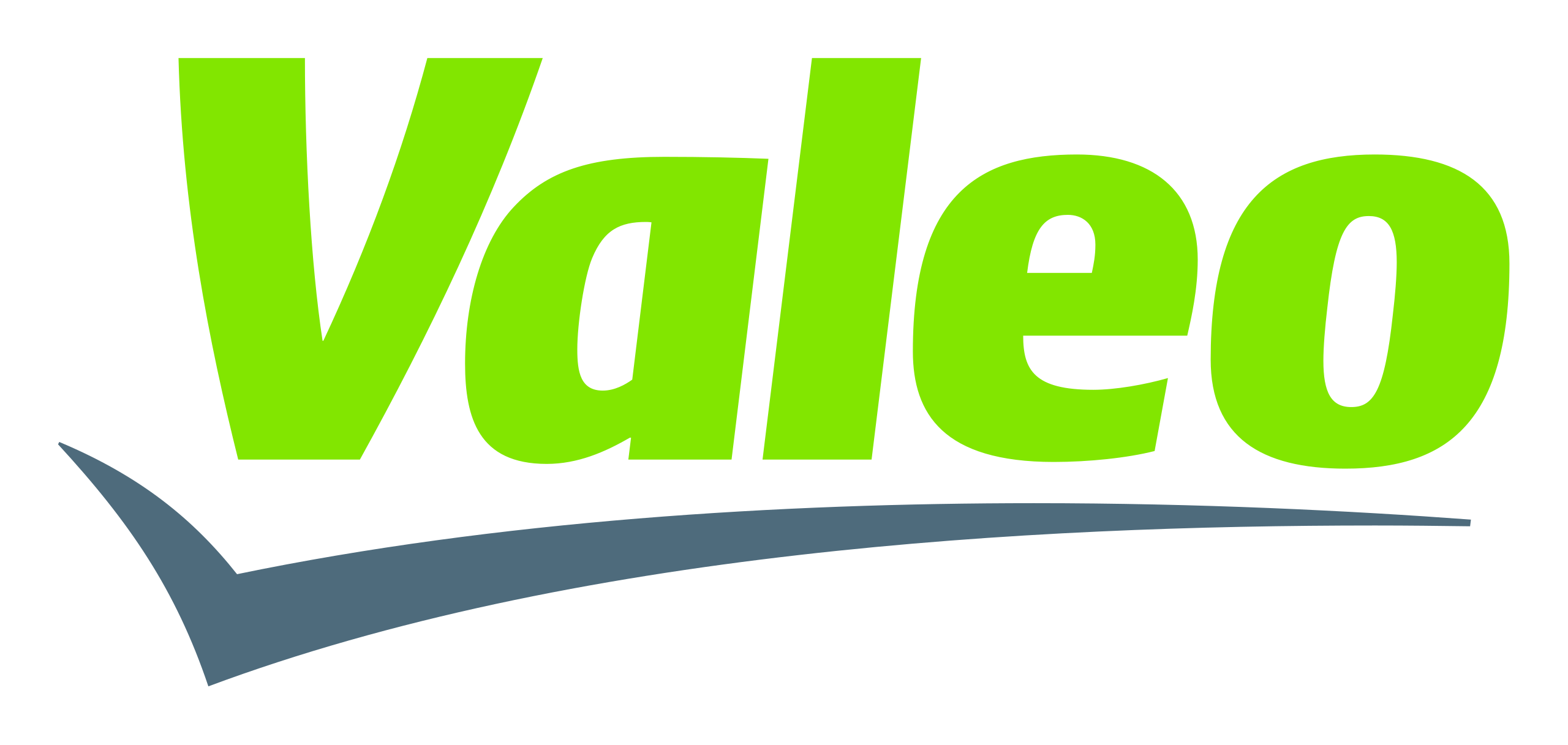
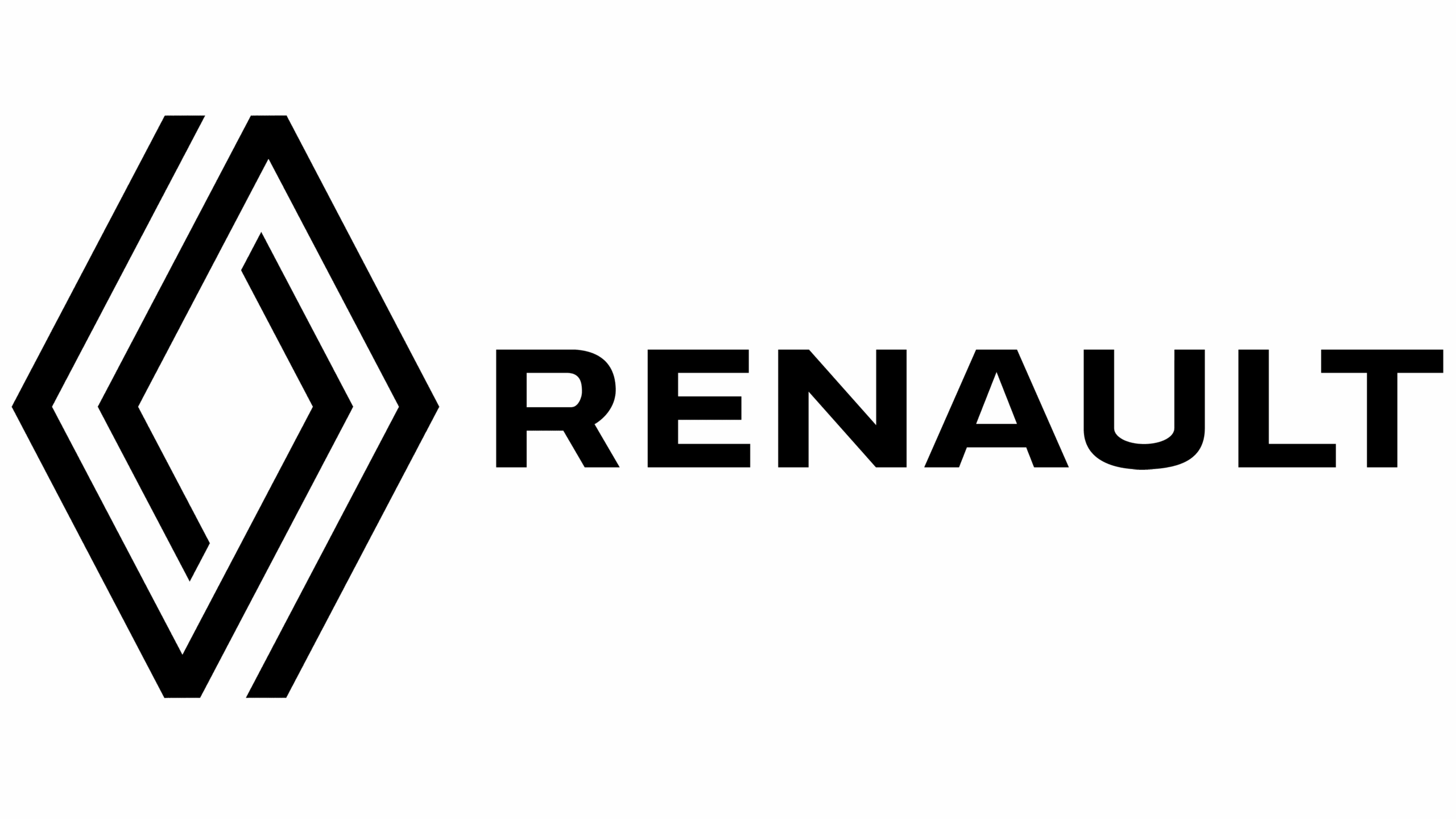
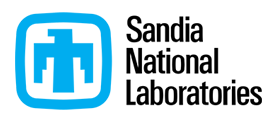
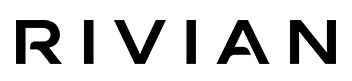
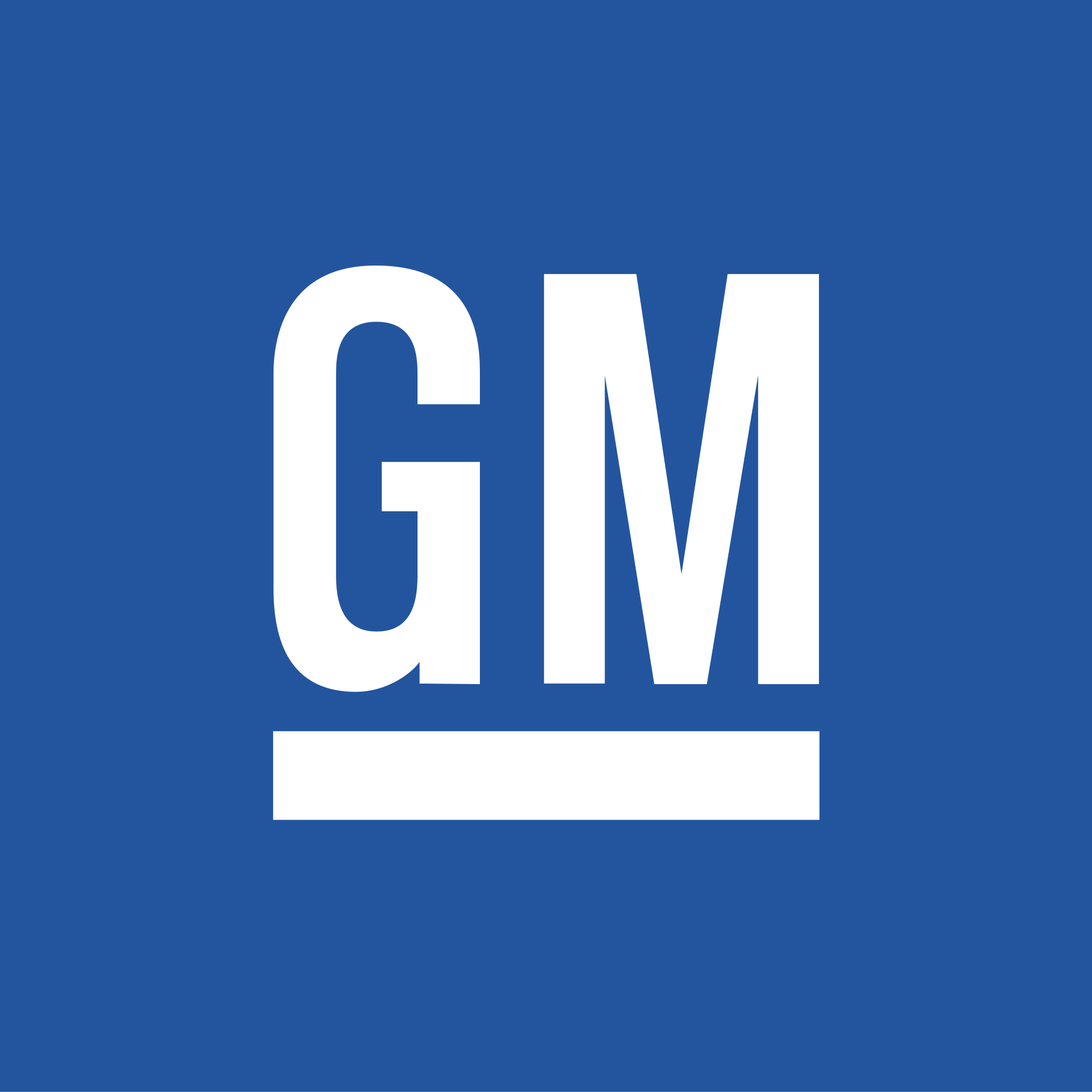
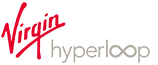
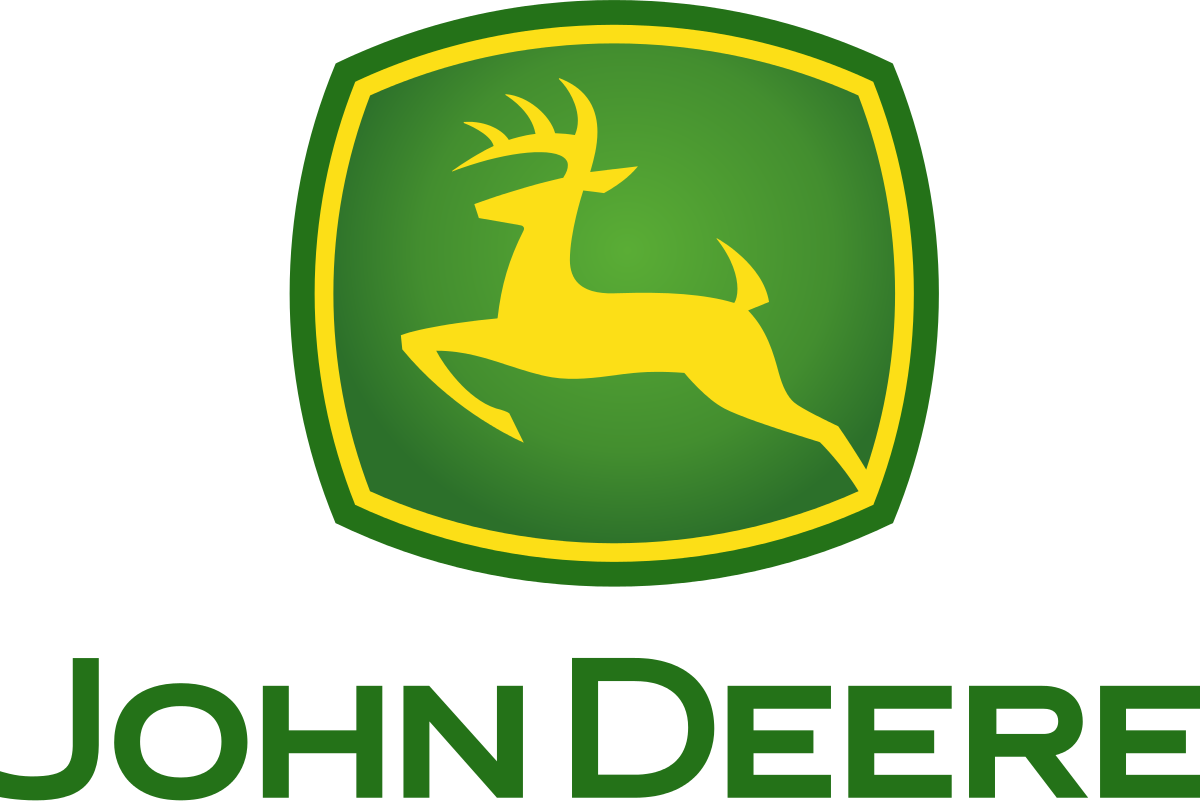
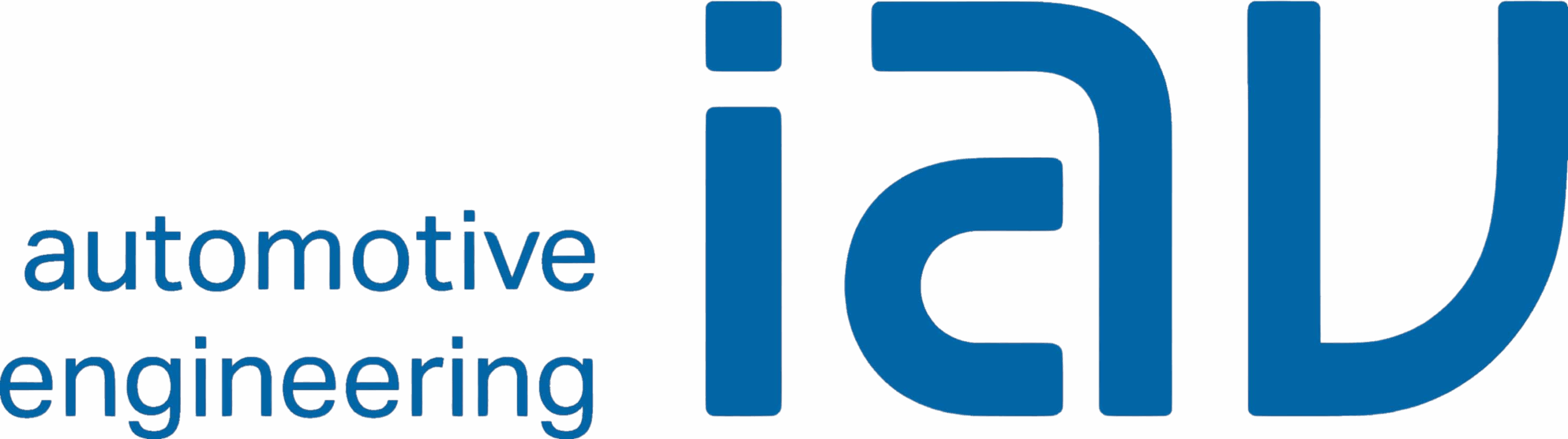
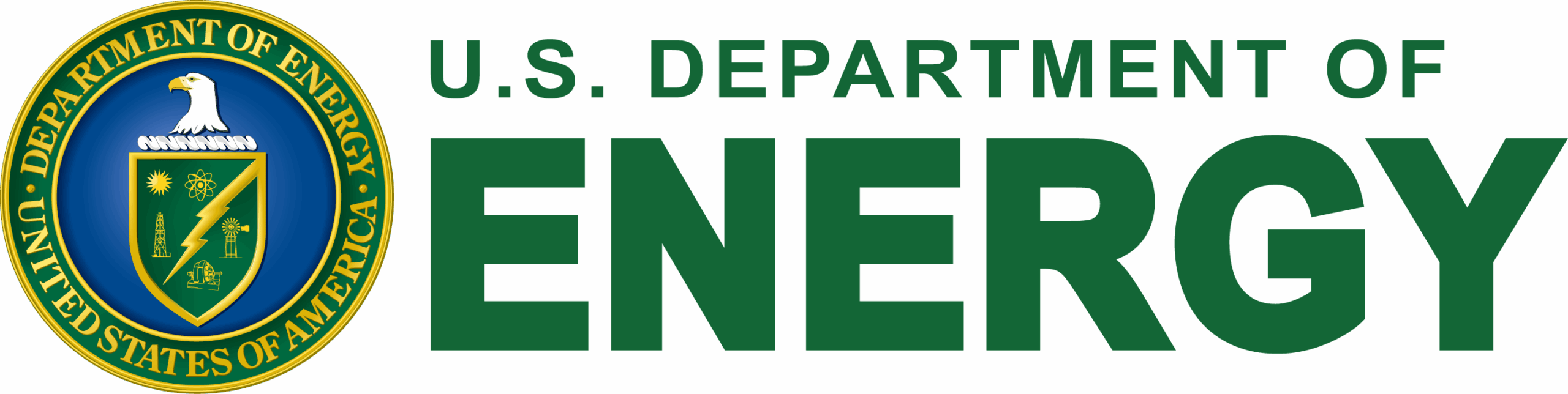
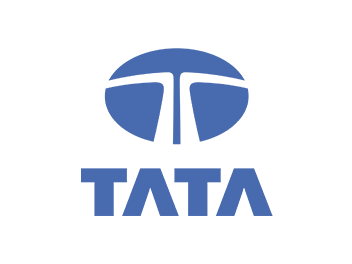
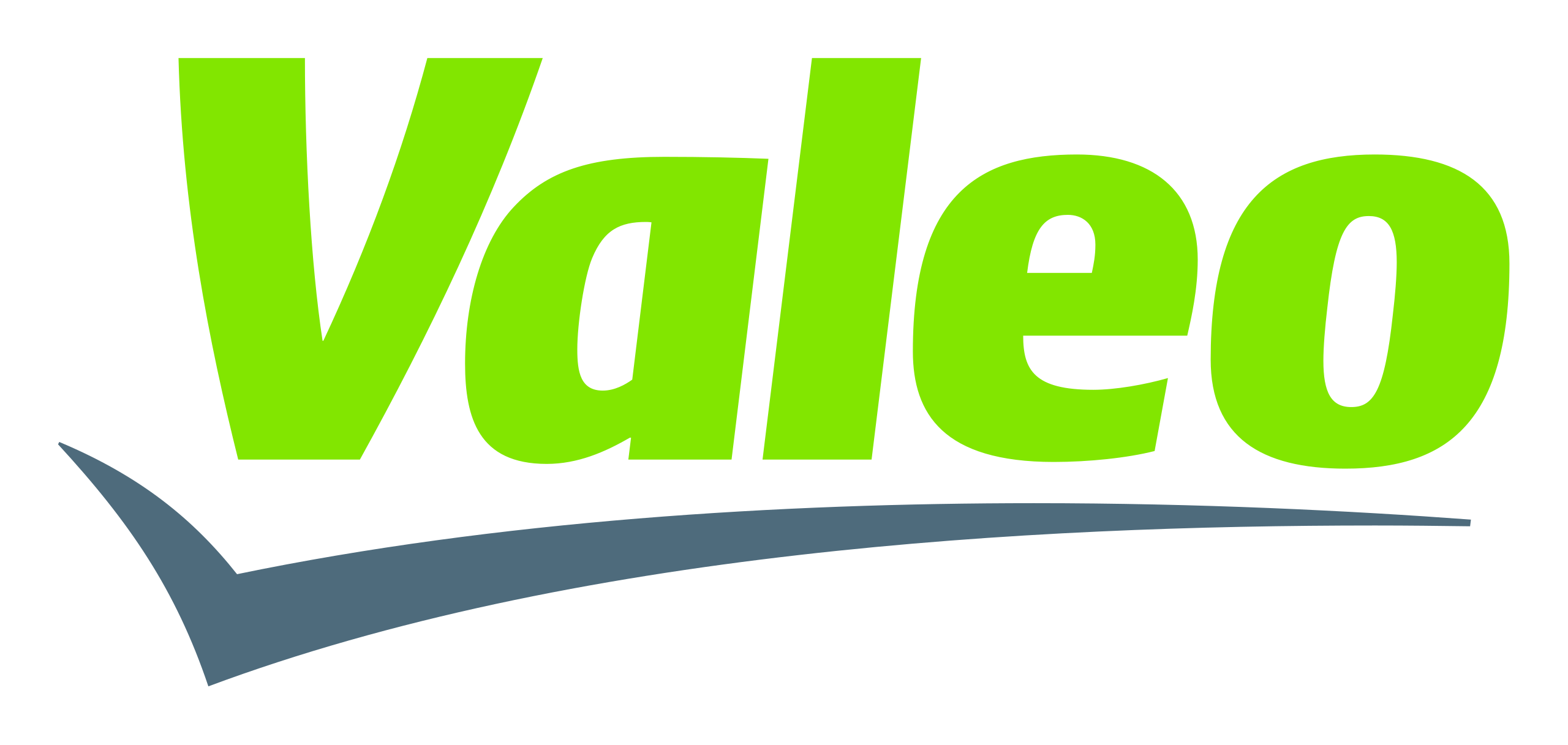
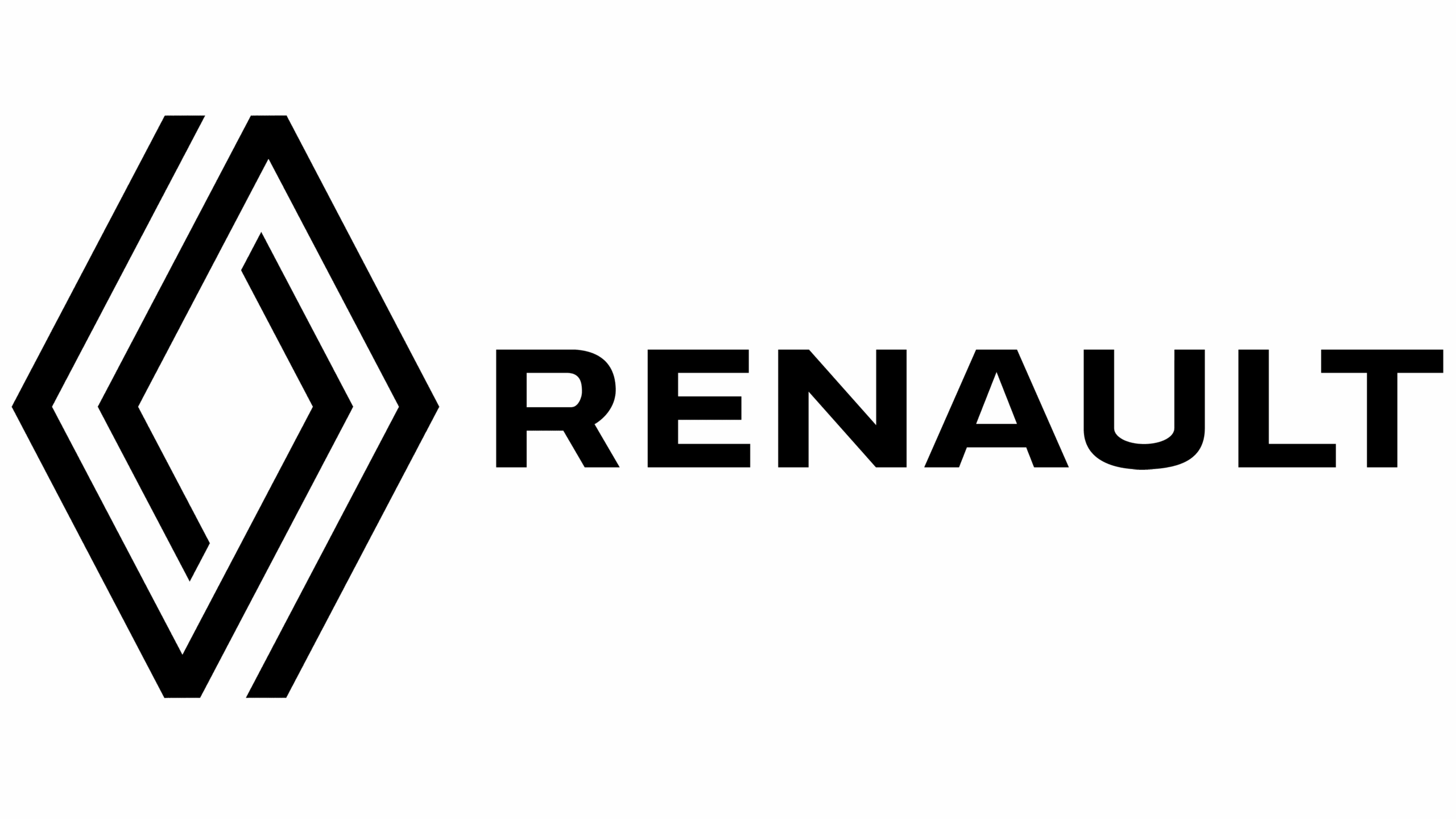
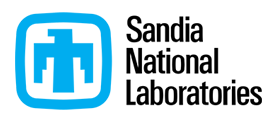
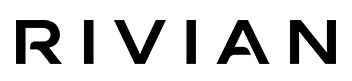
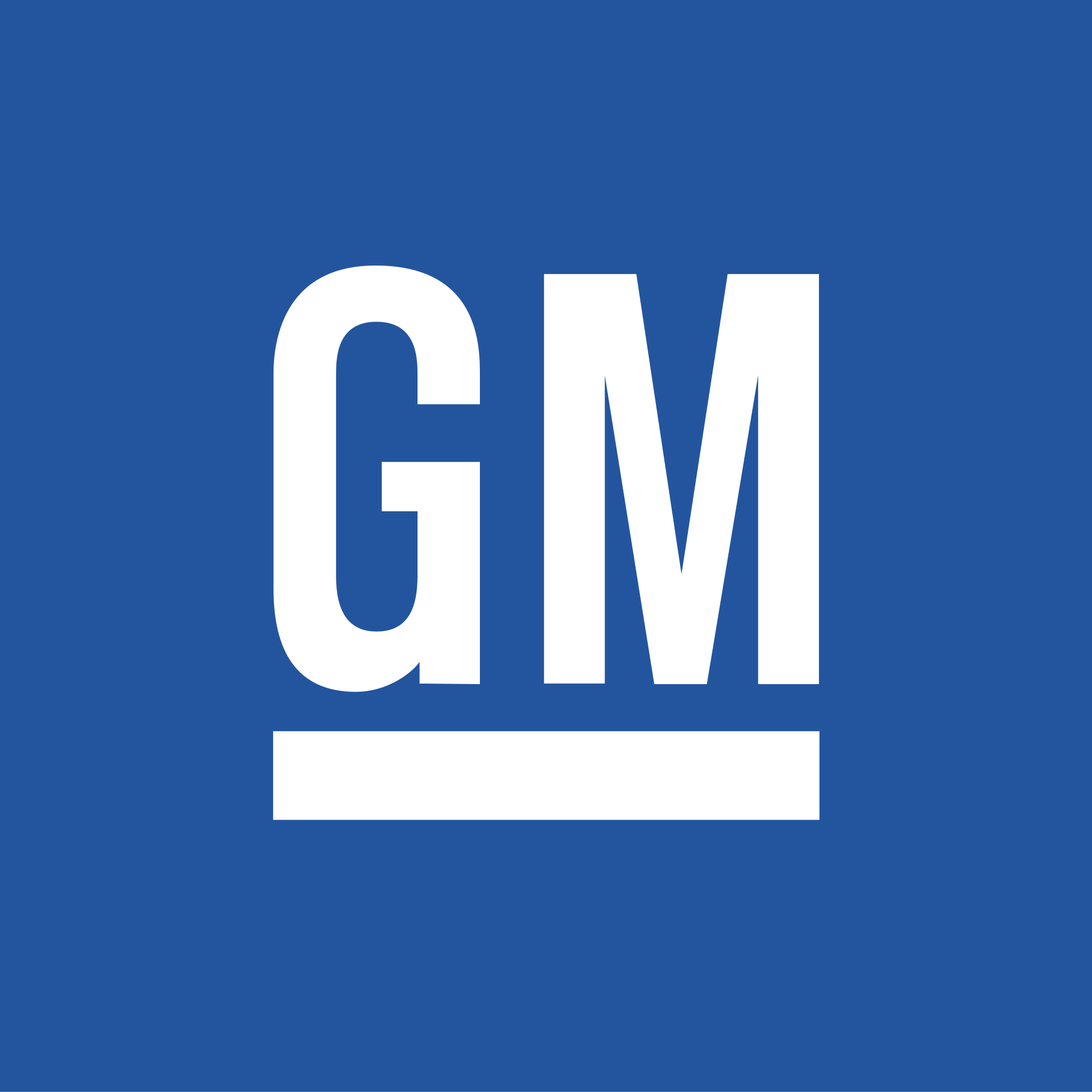
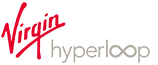
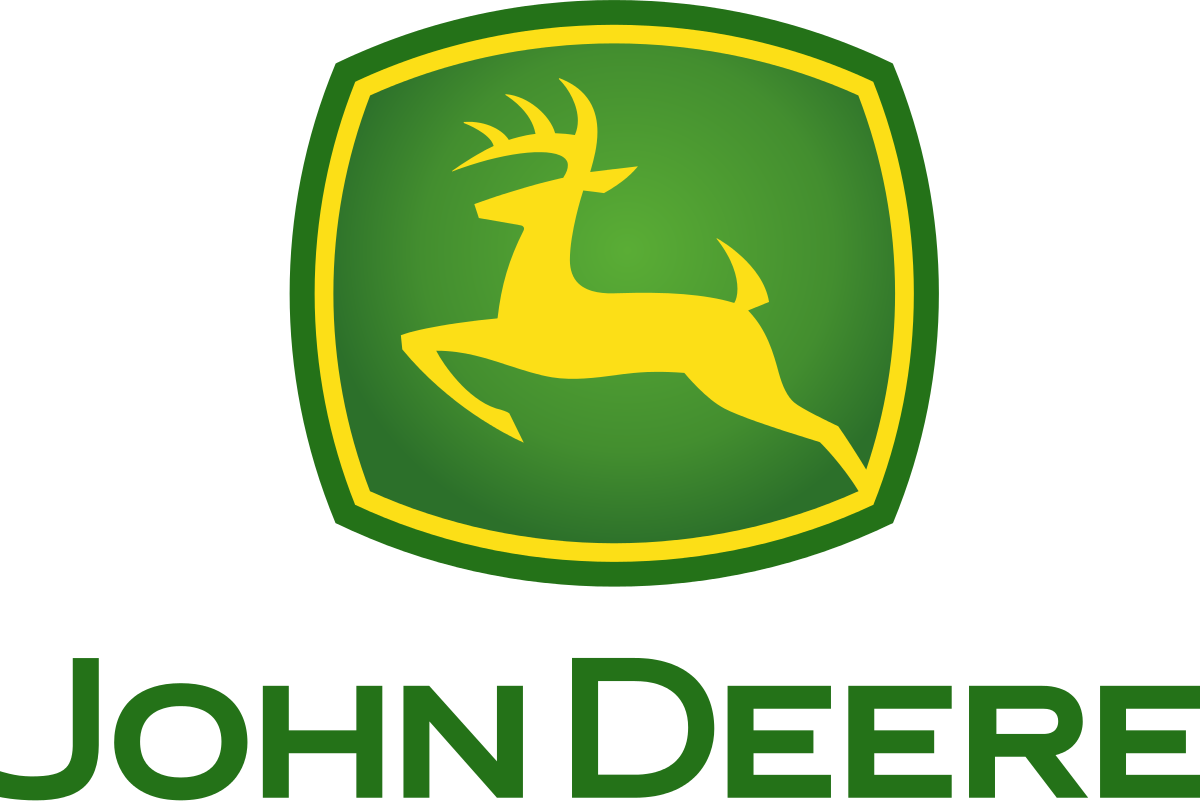
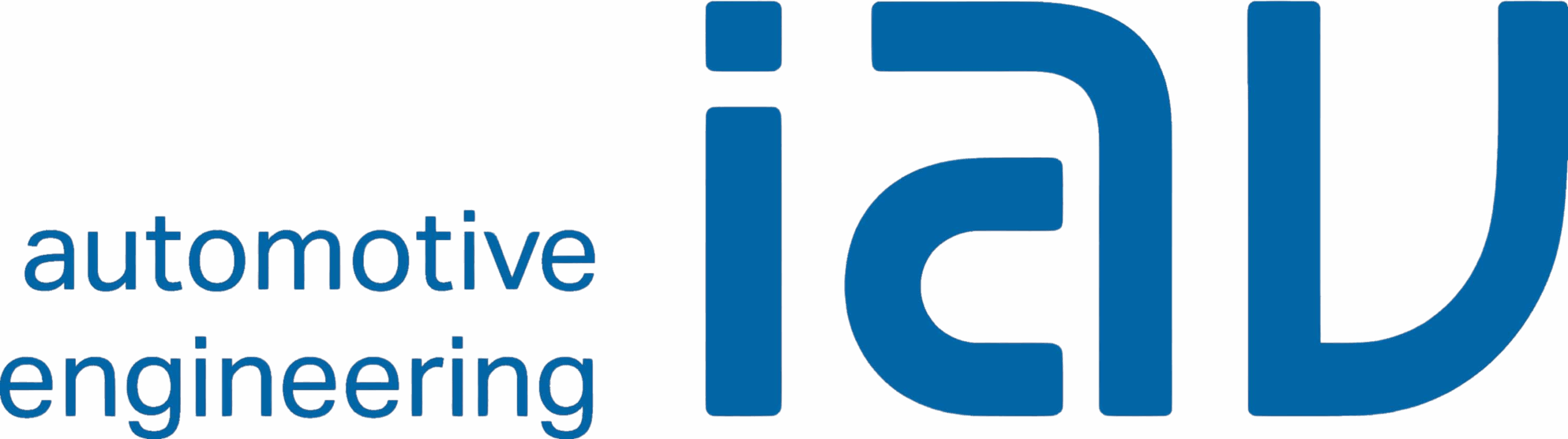
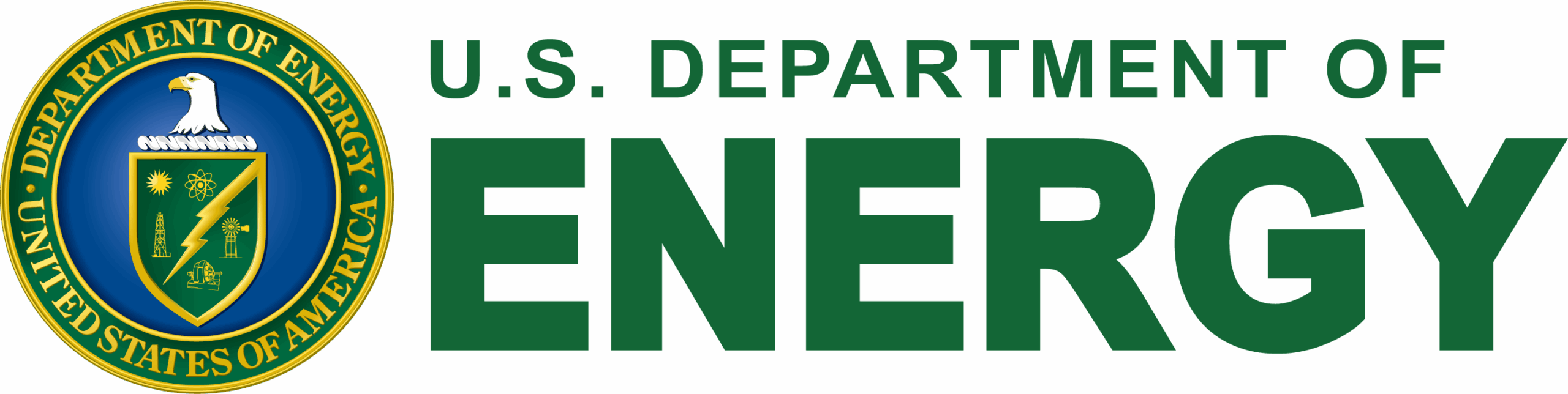
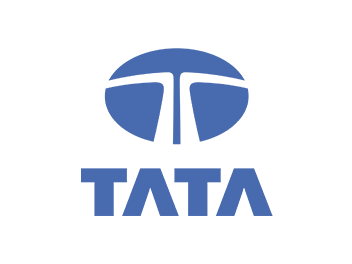
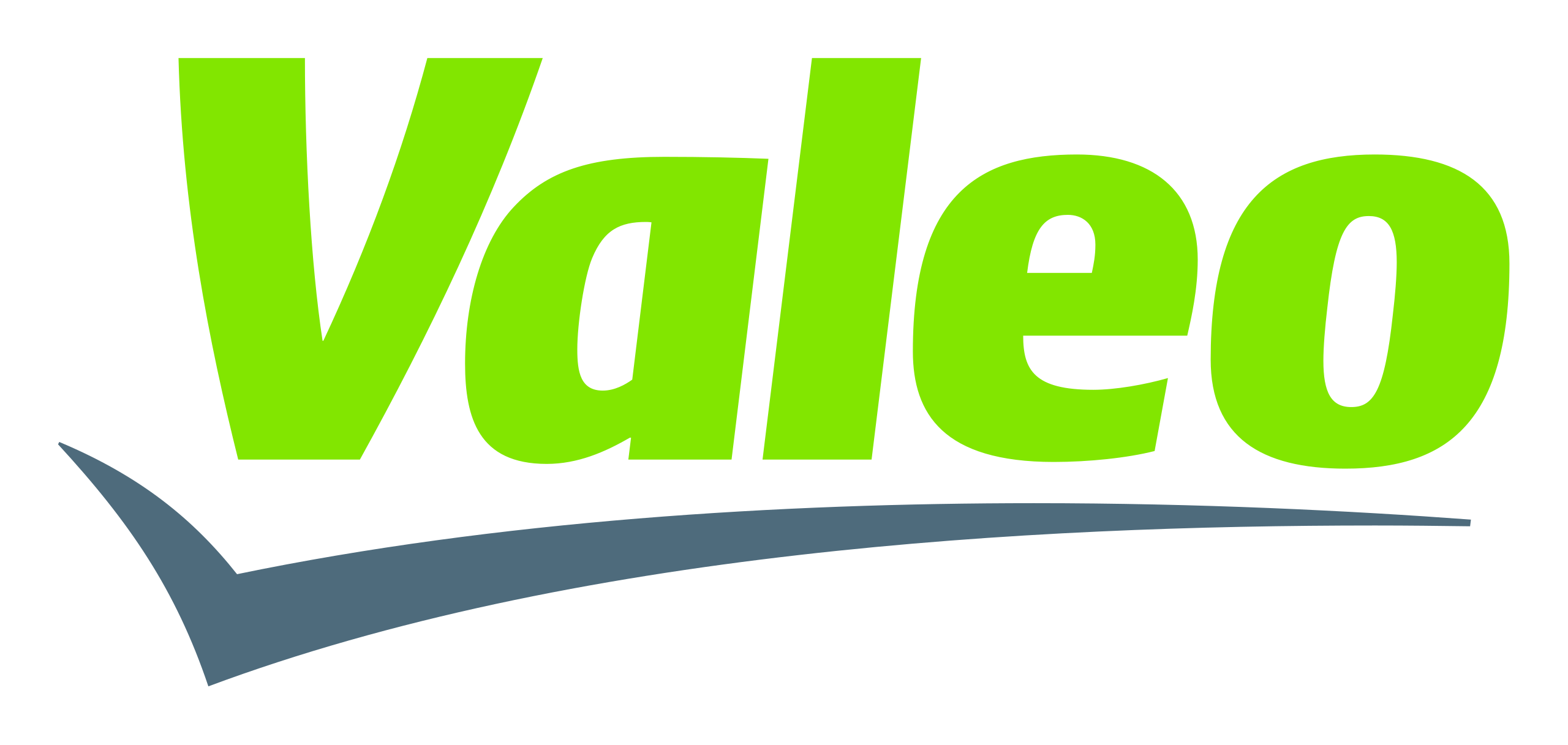
01
Battery management systems
Our BMS approach allows engineers to integrate new technology as soon as it is introduced into the vehicle. Our real-time solution easily migrates existing physical testbeds onto real-time HIL simulation platforms for testing your BMS.
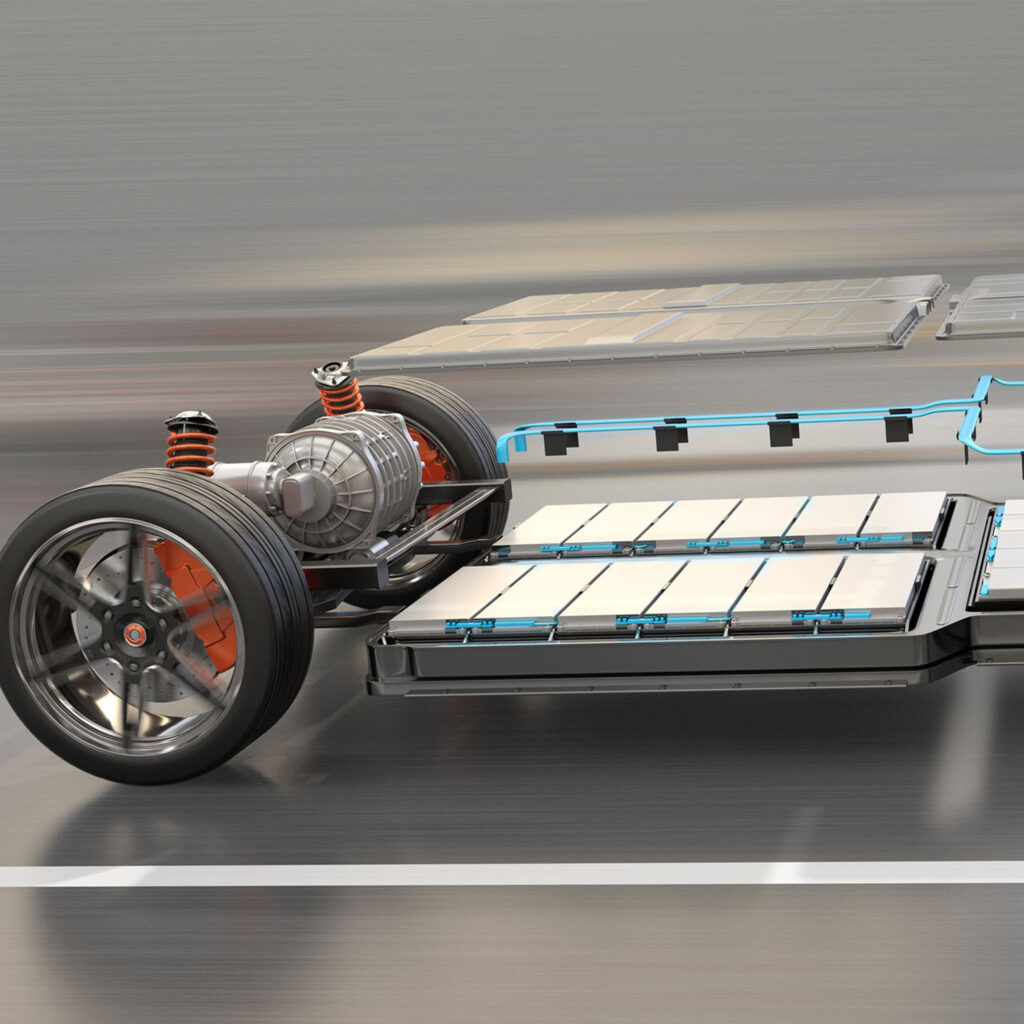
02
Charging
With proven expertise in power systems and power electronics simulation technology and with the highest performance FPGA technology on the market, discover how we can help you address the rigorous testing demands of your charging application with the fidelity you need.
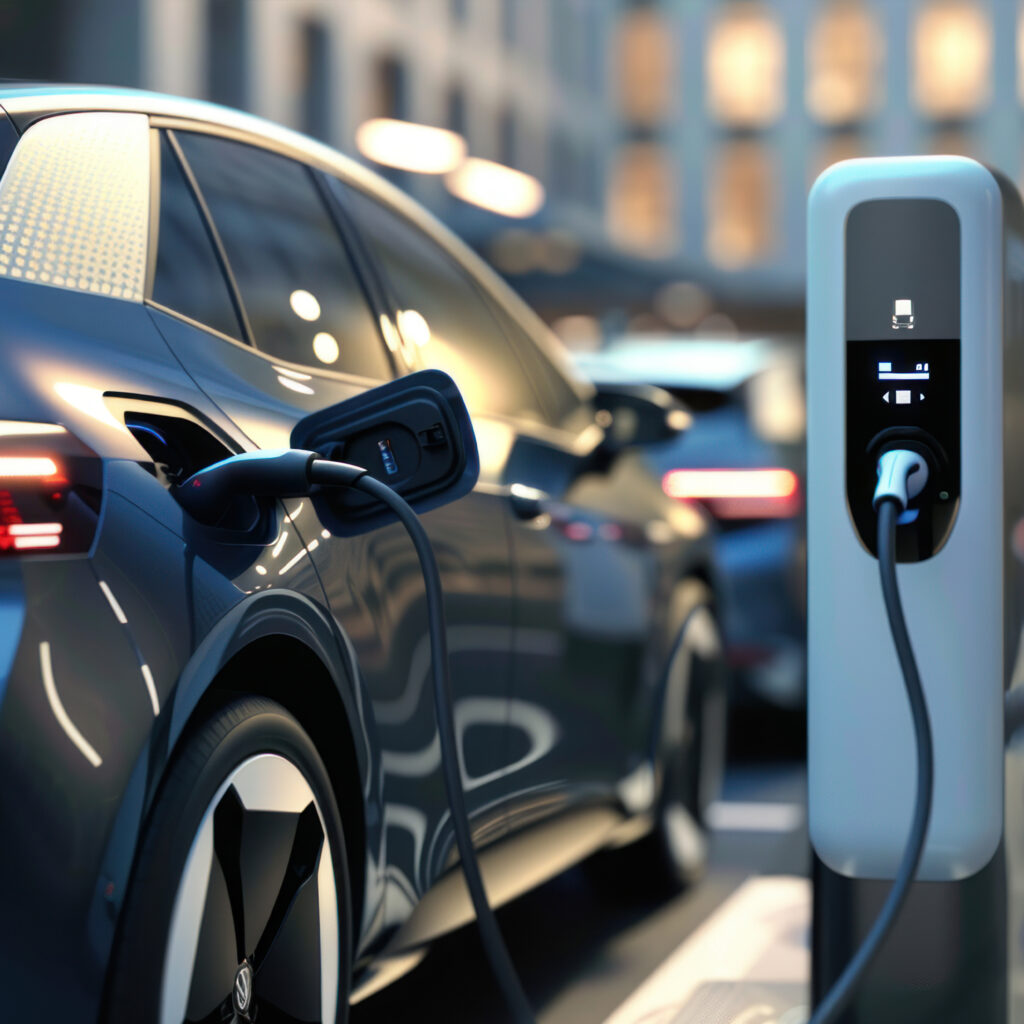
03
Powertrain Systems
OPAL-RT and NI bring you the most powerful, open, and flexible HIL- and PHIL-testing system designed to improve time-to-market and manage system complexity in the rapidly transforming automotive industry.
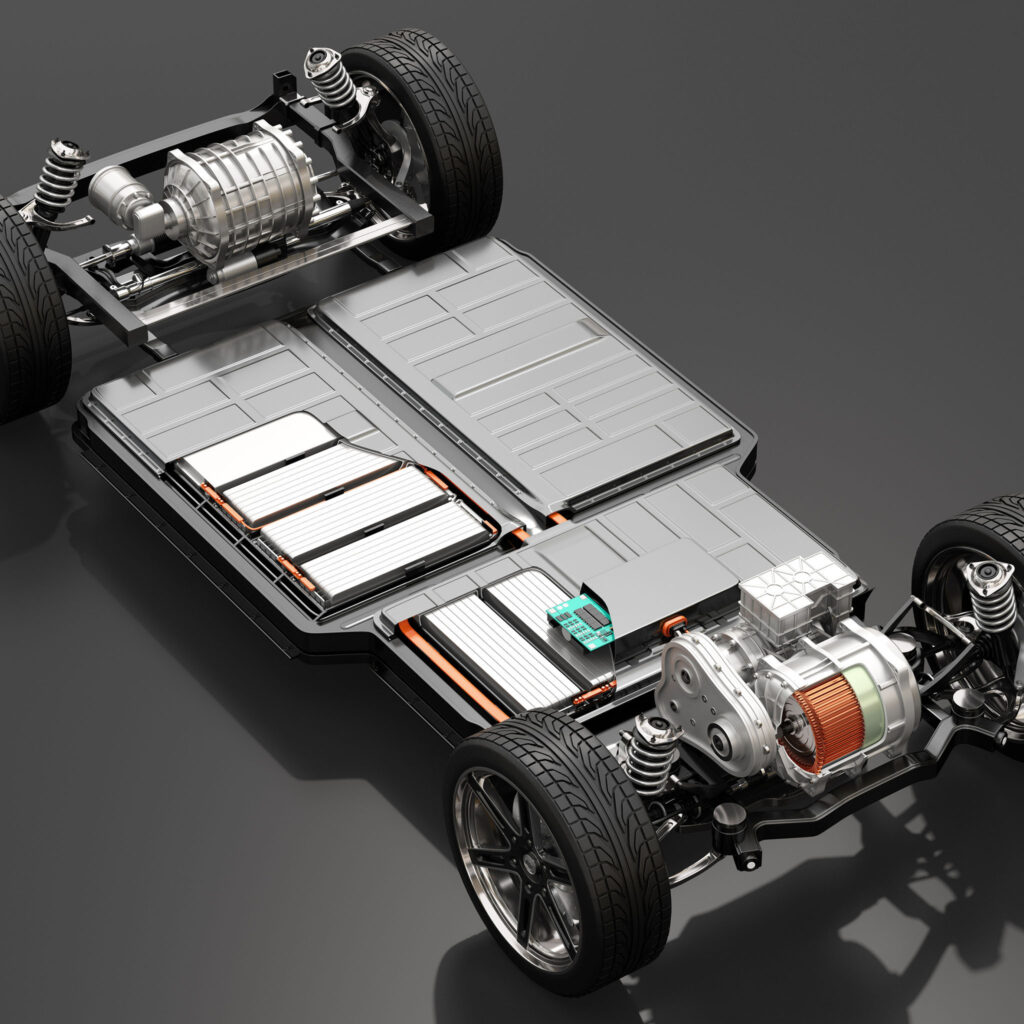
04
Motor emulation
OPAL-RT and D&V combine leading-edge technology and innovative design to produce superior power hardware-in-the-loop (PHIL) simulation for EV/HEV motor drive inverters and DC power system test solutions.
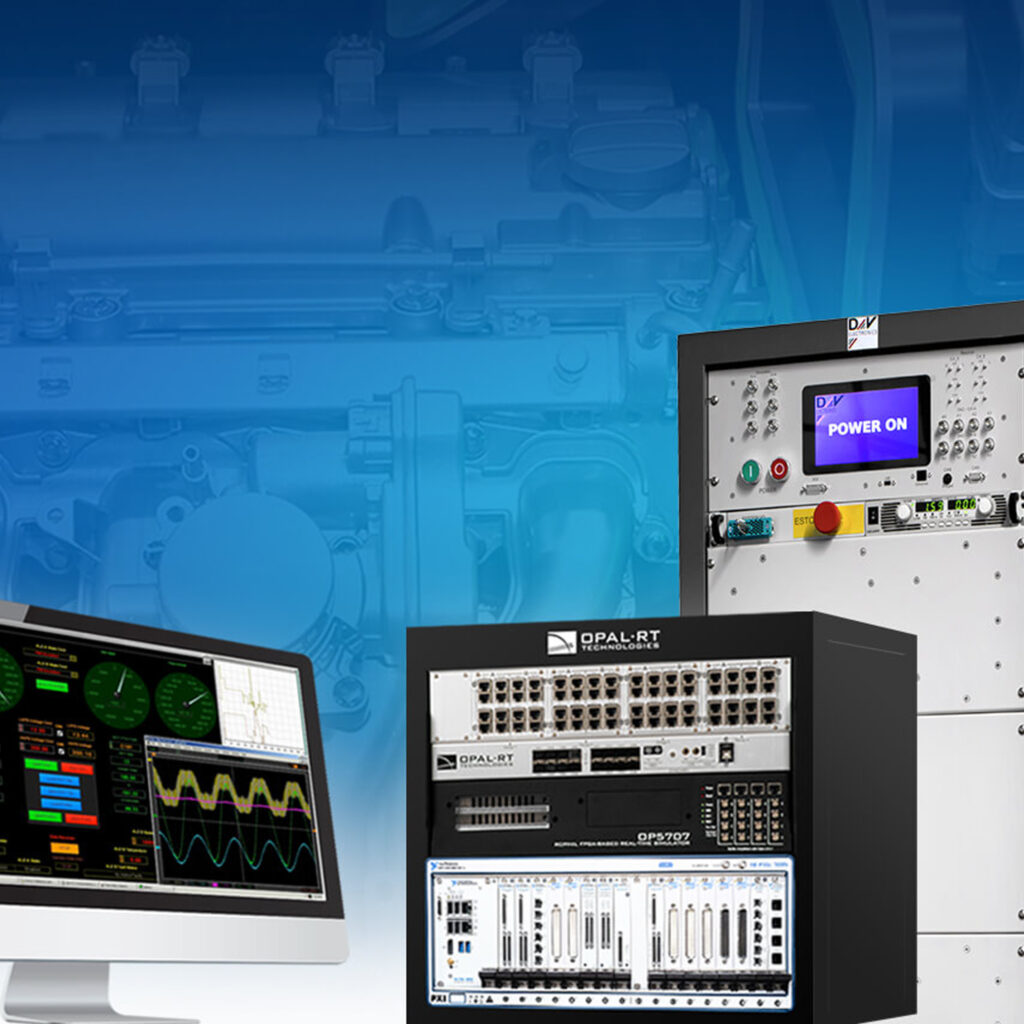