Ford validates hybrid driveline control with real-time HIL simulation
Automotive
09 / 27 / 2016
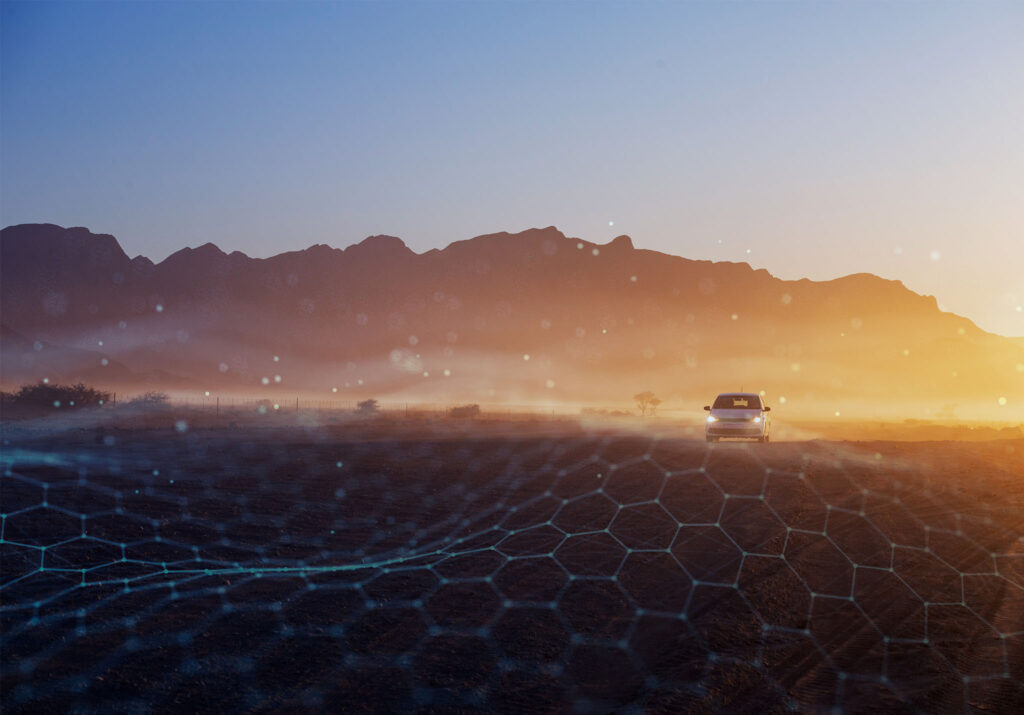
The company
Ford Motor Company is a global automotive manufacturer recognized for its commitment to innovation in hybrid and electric vehicle technologies. The Ford Fusion Hybrid, one of the most successful hybrids on the market and winner of the 2010 North American Car of the Year award, exemplifies the company’s push toward high-efficiency driveline systems backed by rigorous testing and control validation. To ensure its hybrid systems meet strict safety, reliability, and performance expectations, Ford integrates advanced hardware-in-the-loop (HIL) testing into its development workflow.
The challenges
In developing the Ford Fusion Hybrid’s electric driveline, Ford engineers faced complex simulation requirements, particularly with the permanent magnet synchronous motor (PMSM) and its associated inverter. The control system relied on high-frequency PWM signals ranging from 2 to 20 kHz, with dead-times as short as 2 to 20 microseconds—demanding simulation precision well beyond the capabilities of traditional CPU-based systems. The motor drive’s high bandwidth, several orders of magnitude above that of internal combustion systems, required extremely small simulation time steps to maintain accuracy. Adding to the challenge, early-stage testing on physical prototypes risked costly damage, making a robust virtual testing environment essential for developing and validating control strategies under both standard and fault conditions.
The OPAL-RT solution
To meet these demands, OPAL-RT delivered an eDRIVEsim Real-Time HIL Simulator, tailored specifically to simulate PMSM drives and their control behavior with high temporal resolution. Built on a multi-core Intel i7 platform with FPGA-based I/O, the system supported simulation time steps as low as 7 microseconds and digital signal resolution down to 10 nanoseconds. Using OPAL-RT’s Time-Step Averaging Method (TSAM), the simulator handled high-frequency gate signals and switching events with precision—even those shorter than the simulation’s base time step. The system also included support for fault-mode behavior such as high-impedance states, open-phase faults, and natural rectification modes. Ford engineers integrated their production controller with the simulator and performed extensive real-time testing using RT-LAB and the RTeDRIVE Simulink library, distributing subsystems across CPU cores for optimal performance. This setup enabled them to model and simulate each motor drive, boost converter, and power I/O channel independently and in real time.
The results
With OPAL-RT’s HIL platform, Ford successfully tested and validated their hybrid driveline control strategies long before physical prototypes were finalized. They conducted targeted tests such as phase over-current protection, torque-command-based boost converter activation, and speed ramp-up scenarios, all with the controller operating as it would in a real vehicle. The system significantly reduced development time and cost, improved product quality, and allowed engineers to explore edge cases and fault scenarios with no hardware risk. Most importantly, the simulator provided the temporal precision and model flexibility needed to support high-bandwidth electric motor drives—ensuring Ford’s hybrid control systems could be refined, validated, and delivered to production with confidence.