HIL and RCP simulation systems for wind turbine laboratory
In partnership with Festo, we’ve developed a premier laboratory that enables academic researchers and teachers to conduct tests and teach using the ideal hardware-in-the-loop (HIL) and rapid control prototyping (RCP) simulation systems. The lab is ideally suited for work in electrical machinery, power converters, and wind energy generation.
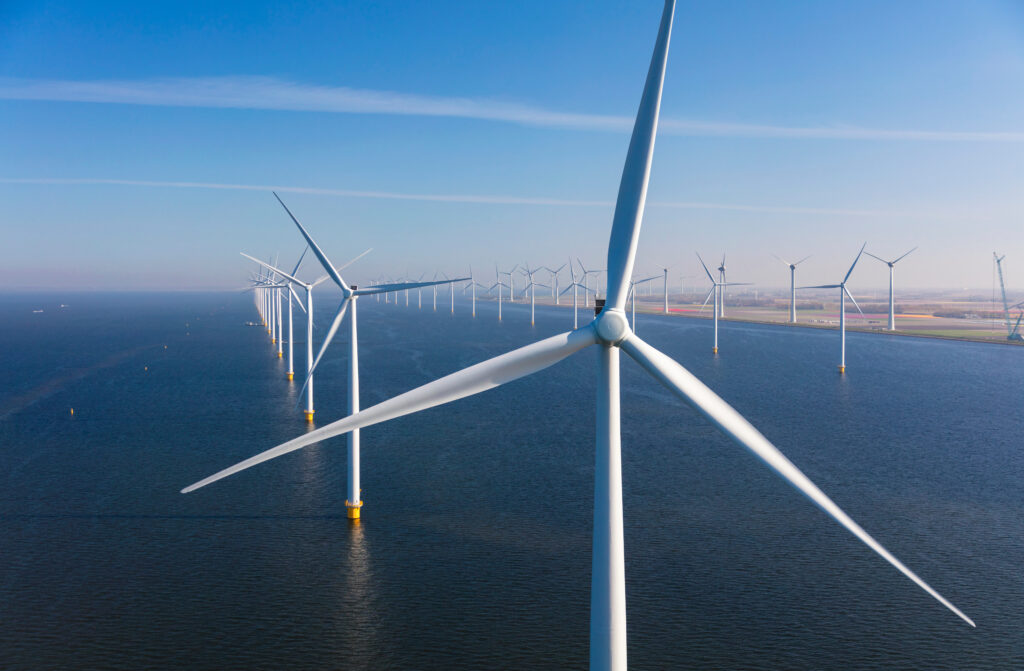
Solution
A versatile platform for teaching and testing control algorithms
Our real-time simulators can be seamlessly interfaced with Festo’s 2 kW doubly-fed induction generator (DFIG) laboratory kit to help you achieve your research and teaching objectives. The two Festo 6-pulse IGBT modules are controlled directly by our simulator’s FPGA, and the Simulink® model can be modified easily to test various types of control algorithms. This solution is also ideal if you already have your hardware, such as IGBT or motors, as they can be easily interfaced with the simulator.
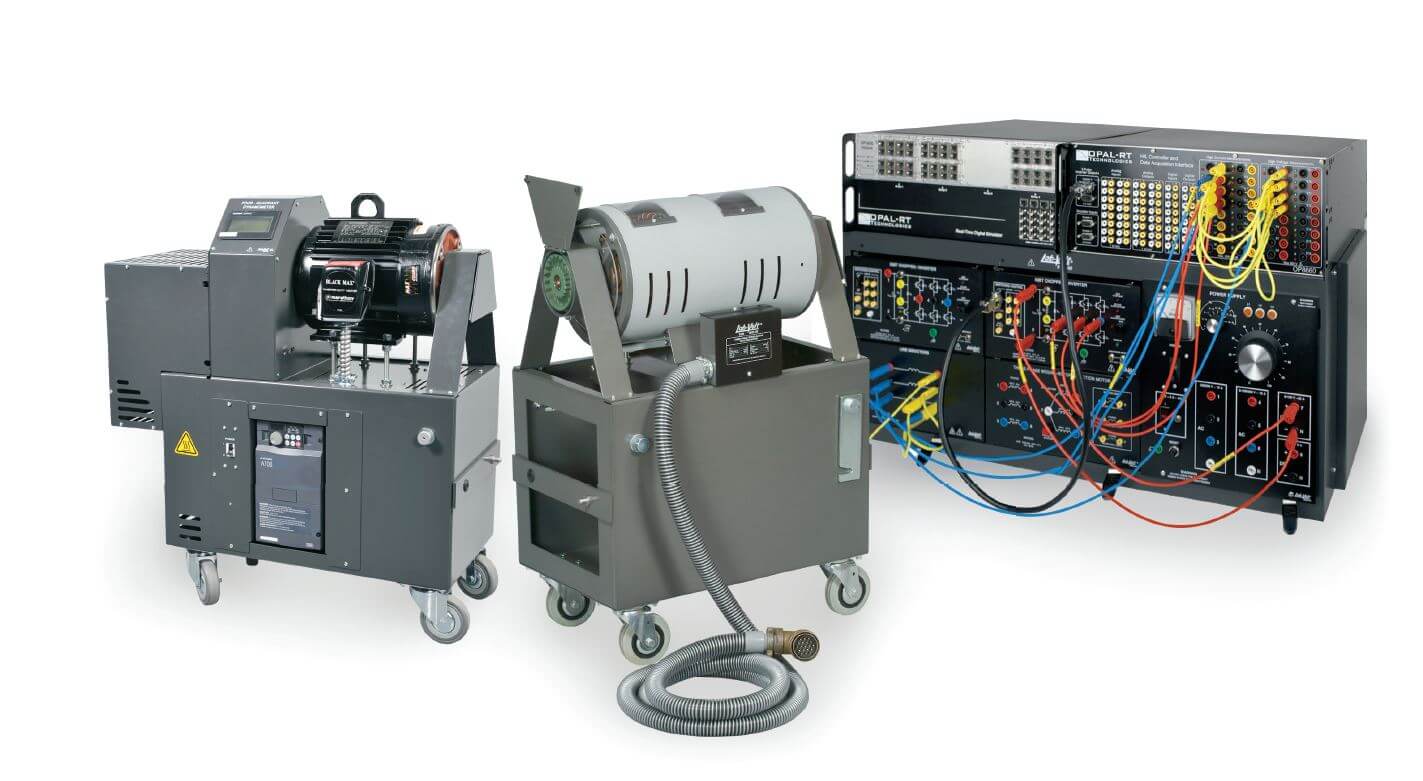
Curriculum goals
V-cycle learning in electric motor control laboratories
HIL and RCP make it possible to test, validate, and reduce controller development in a secure environment. Our system, combined with Festo’s hardware, enables you to fully teach the V-cycle principles used in the industry. Students and researchers can build a model and then validate the same model against a real system.
Rapid control prototyping (RCP)
With RCP, the plant is real (real IGBT or generators) and the controller algorithm is running inside the real-time simulator. This configuration enables one to quickly test different control algorithms without worrying about the controller’s platform used, like DSP or FPGAs. Users can focus on the algorithms instead of spending a precious amount of time debugging and implementing the algorithm inside a proprietary platform (DSP). In short, the real-time simulator makes it easy to go from Simulink® models to a real working prototype in a few clicks.
Hardware-in-the-loop (HIL)
With HIL, the controller is real and the plant is virtual. It is not always practical to do controller development on a real system for multiple reasons like security, availability, and the high risk of damaging the equipment. HIL makes it possible to test the control against a safe and accurate virtual model before connecting to the real plant.
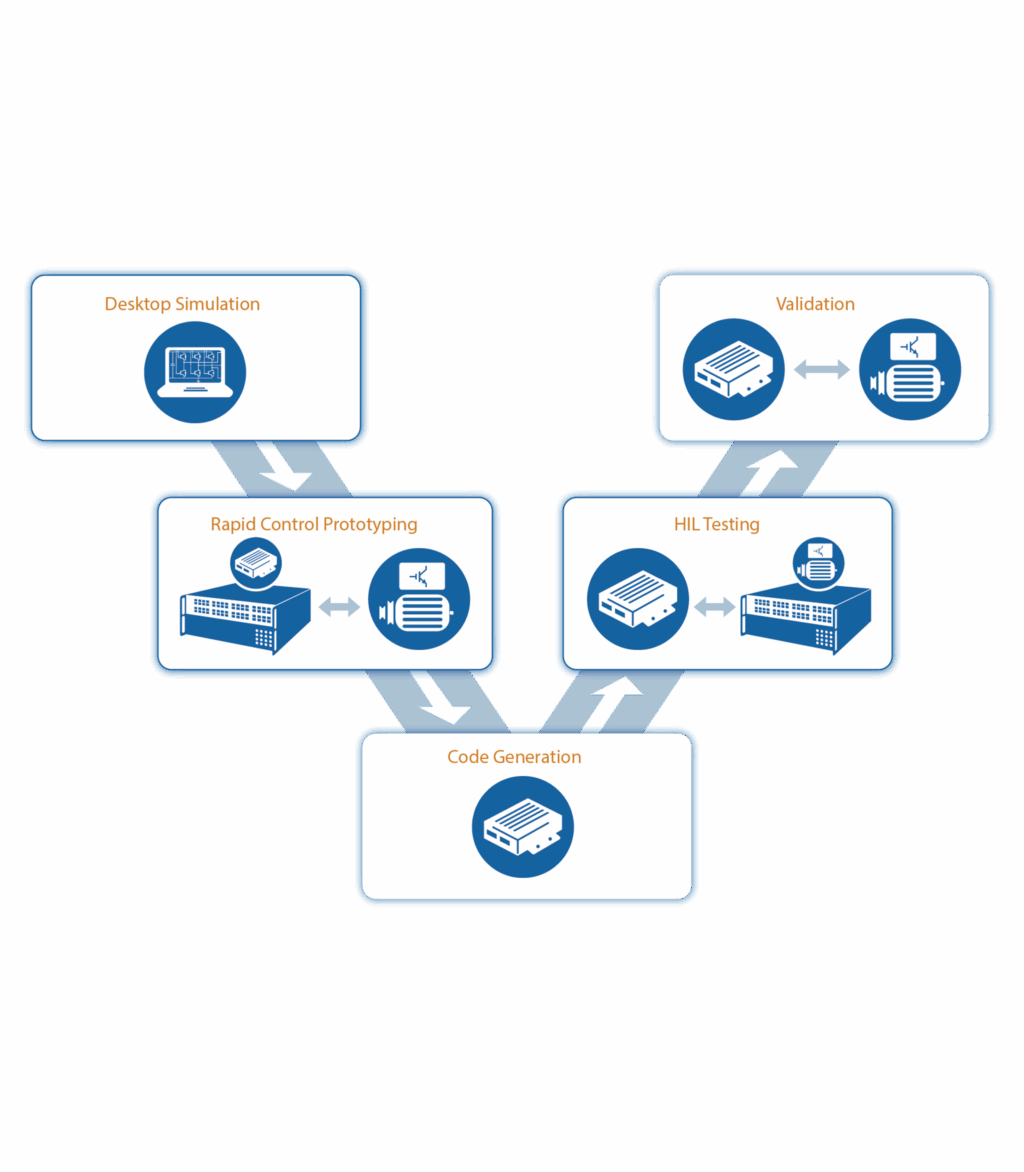
Benefits
Why choose our laboratory
We set the standard for simulation technology with our experience and cutting-edge solutions. Our commitment to innovation allows us to deliver reliable, high-performance tools tailored to meet your needs.
01
Study, design and test
Test power electronics controls, validate models with experiments, integrate renewables into the grid, and assess system behavior under all conditions.
02
Integrated tools for control design
Use RT-LAB, MATLAB/Simulink®, Simscape, and Stateflow with full Festo lab integration and OPAL-RT simulators. Tutorials and demos included.
03
Built for education and speed
Enjoy fast setup, flexible configuration, broad experiment coverage, and strong support. Scalable and customizable for any need.
04
Trusted by industry leaders, driven by innovation
With over 25 years of experience, we deliver real-time simulation solutions that push the boundaries of technology and help you build the future with confidence.
Integration
Easy integration with your curriculum
The kit is delivered with a series of working examples and case studies that easily integrate with your curriculum.
Renewable energy
- Doubly fed induction generation
- Inverter control (6-pulse IGBT)
- Back-to-back inverter control
- DC bus active and reactive power control
Closed-loop motor control models
- Permanent magnet DC motor speed control
- Squirrel cage induction machine speed Control
- Permanent magnet synchronous motor speed control
- Permanent magnet synchronous motor flux angle correction
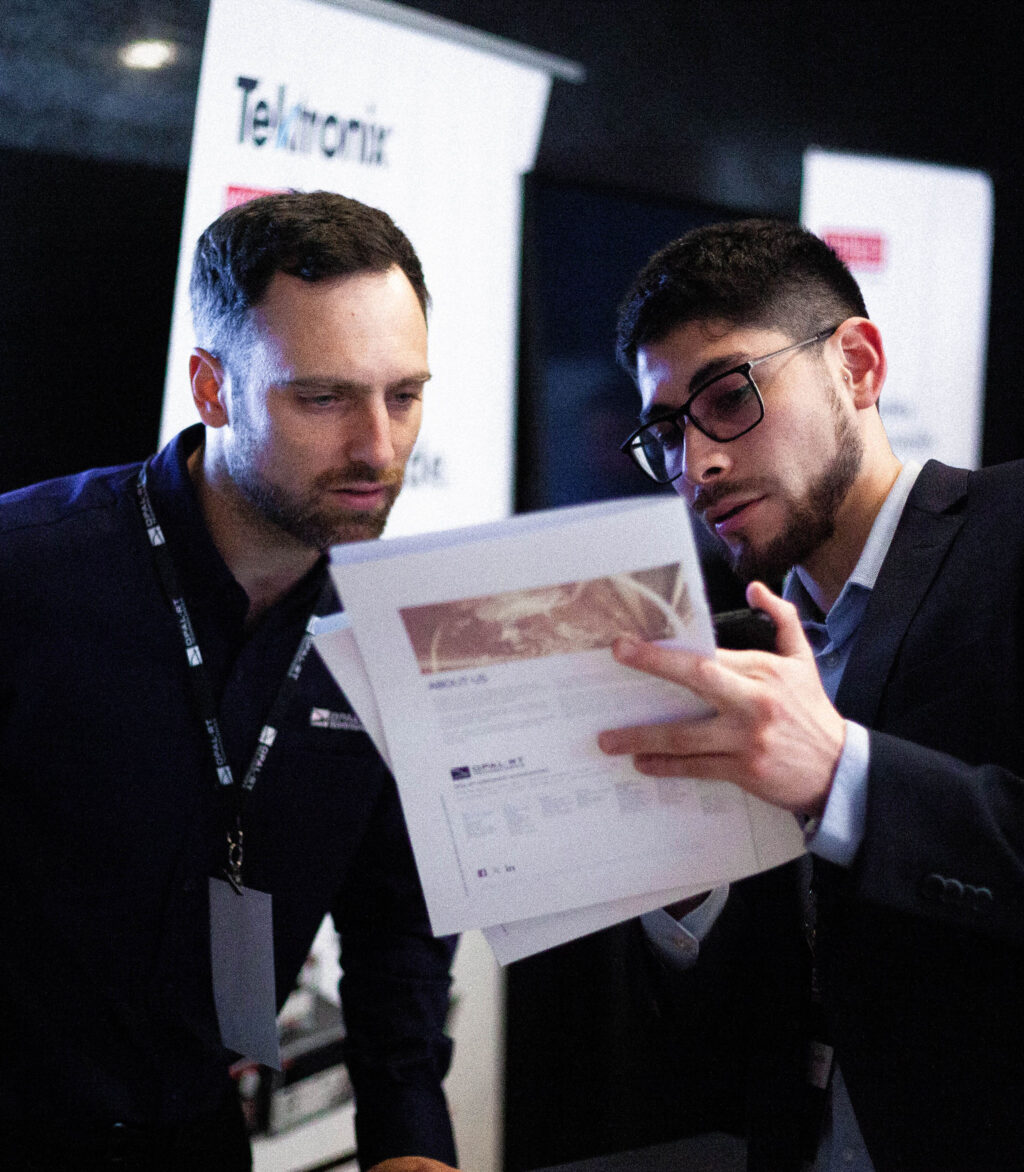