Power hardware-in-the-loop testing
Power hardware-in-the-loop (PHIL) simulation builds on HIL by introducing real power exchanges between simulated and physical systems. It enables safer, faster, and more flexible testing of power electronics and power systems, empowering engineers to test real devices under real-world conditions without compromise.
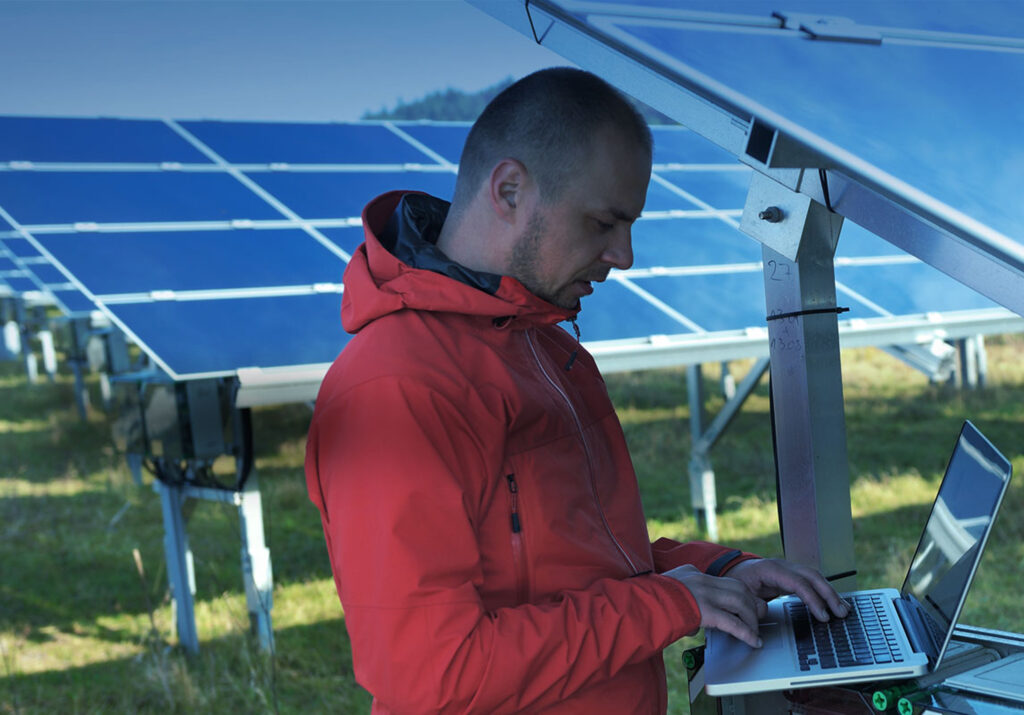
A smarter approach to high-power testing
Why PHIL simulation is reshaping the future of power system validation
Traditional testing of high-power equipment—like converters, generators, and motors—requires physical setups that are costly, complex, and often unsafe. Power hardware-in-the-loop (PHIL) changes the game by replacing the physical power system with a high-fidelity, real-time simulation, while still interacting with actual hardware through a power interface.
By integrating a power amplifier between the simulator and the device under test (DUT), PHIL allows for bidirectional power exchange, offering closed-loop testing that captures the dynamics of real-world operation. As a leading solution for hardware in the loop power electronics validation, the result is faster development, higher confidence, and reduced risk.
Solution
How power hardware-in-the-loop works
PHIL simulation enhances standard HIL by enabling real power flows between the simulator and the DUT. As part of our power hardware in the loop platform, a power amplifier connects to the simulator’s low-level signals and boosts them to the required voltage and current levels. Feedback from the DUT is measured and returned to the simulator in real time to maintain the closed-loop system. This process allows engineers to simulate demanding scenarios—like fault conditions or load variations—and study the DUT’s behavior with unmatched safety and precision.
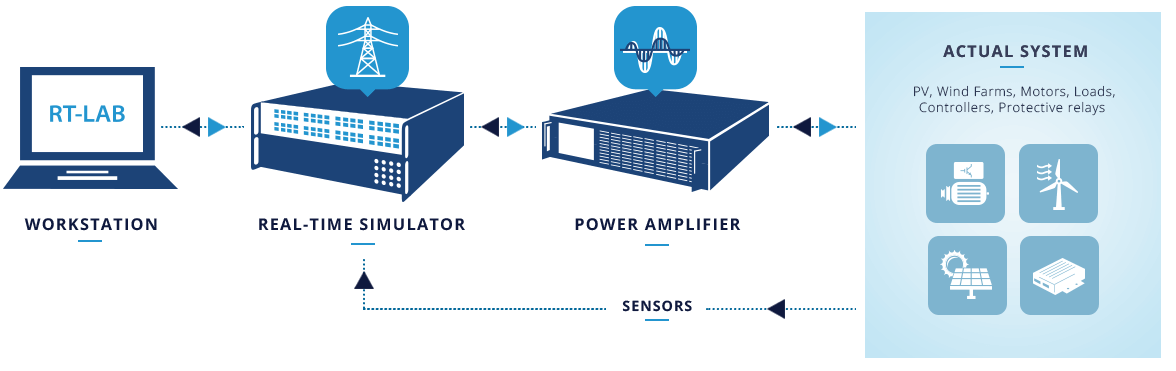
Benefits
Safer, faster, and more flexible high-power testing
PHIL simulation provides all the advantages of HIL, plus real power exchanges, unlocking a new level of insight and performance validation.
01
High performance
Run high-fidelity power electronics and system simulations with exceptional accuracy, low distortion, and minimal phase lag—comparable to analog benches or dynamometers.
02
Flexible and efficient testing
Easily test a broader range of conditions, characteristics, and fault scenarios with reduced setup and maintenance time.
03
Enhanced safety
Perform tests that would be dangerous or impractical in real life, like fault injection or inverter thermal testing, without risking hardware damage.
04
Accelerated validation
Speed up development cycles by streamlining testing and validation, reducing reliance on complex physical setups.
Considerations
Choosing the right power amplifier for your PHIL project
Selecting the right amplifier is crucial to the success of your PHIL setup. Consider:
- Closed-loop stability and fidelity
- Power range and voltage/current capacity
- Source/sink capability
- Bandwidth and phase margin
- Integration with real-time simulation platforms
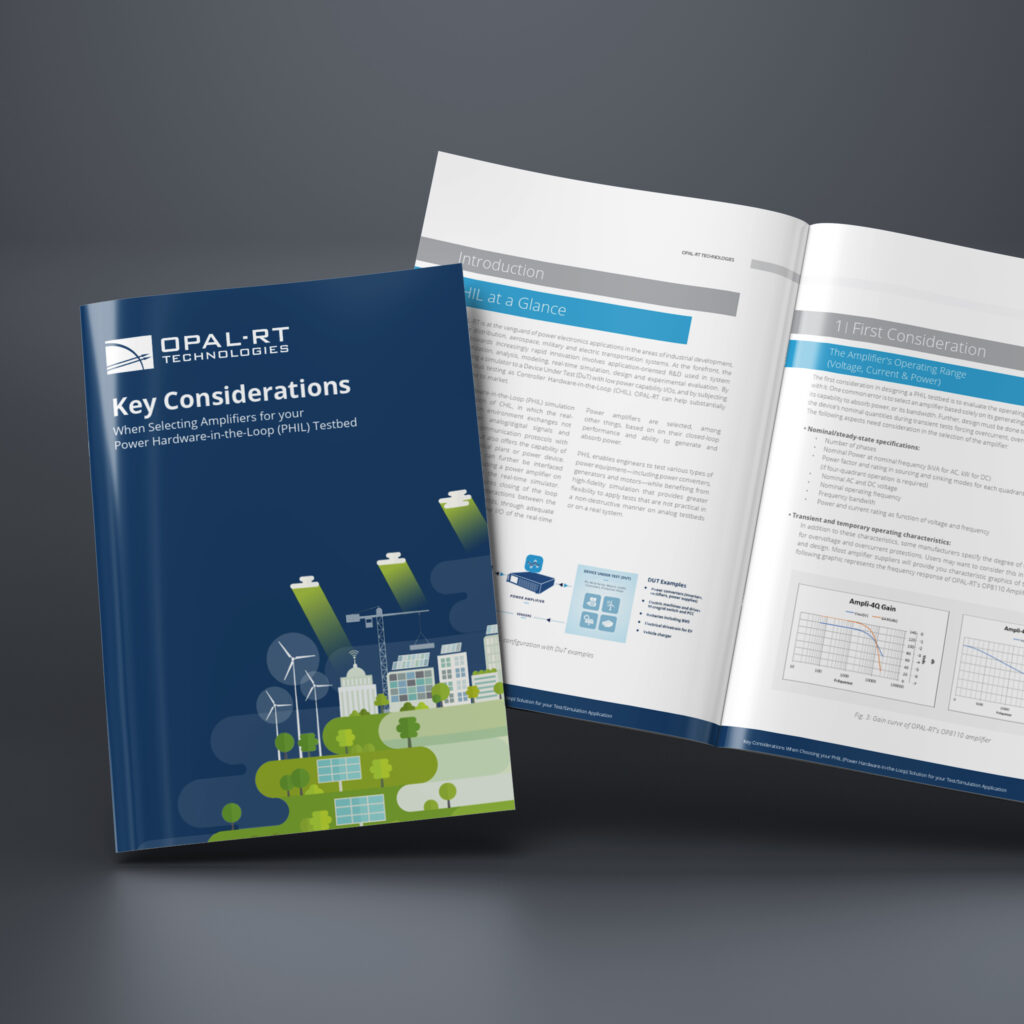
Applications
Used across industries
PHIL simulation is a critical tool in any domain where control, protection, or monitoring systems are developed. It’s trusted by engineers, researchers, and educators to de-risk testing and accelerate innovation.

Energy
Validate protection, stability, and integration of renewables
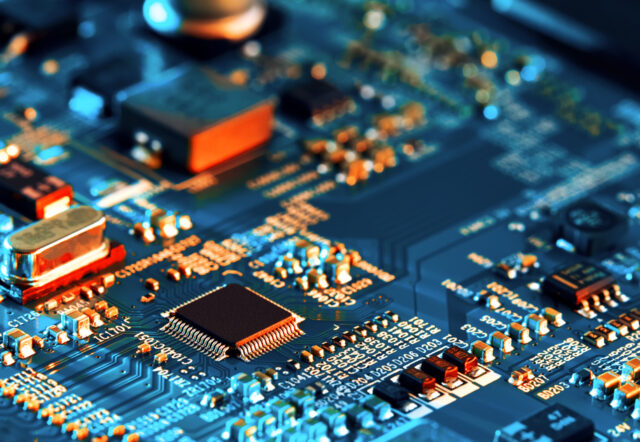
Power electronics
Test converters, inverters, and power systems dynamically
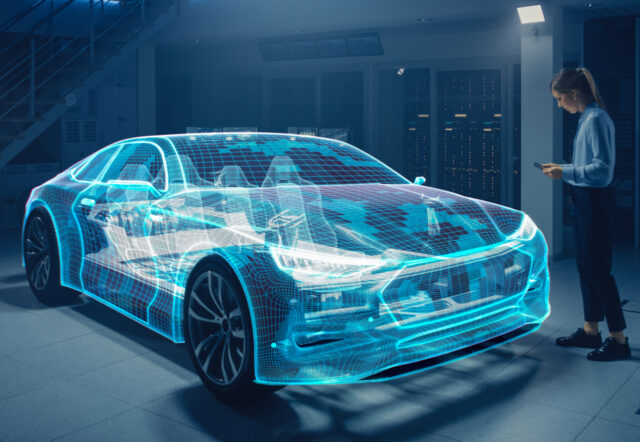
Automotive
Develop EVs, battery management, and driver-assist systems
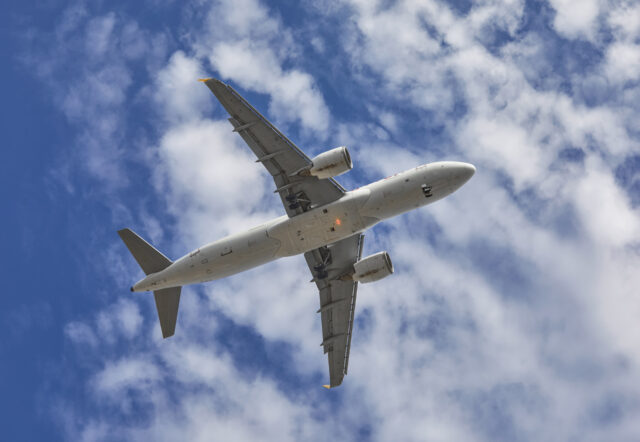
Aerospace
Simulate flight control, avionics, and propulsion systems
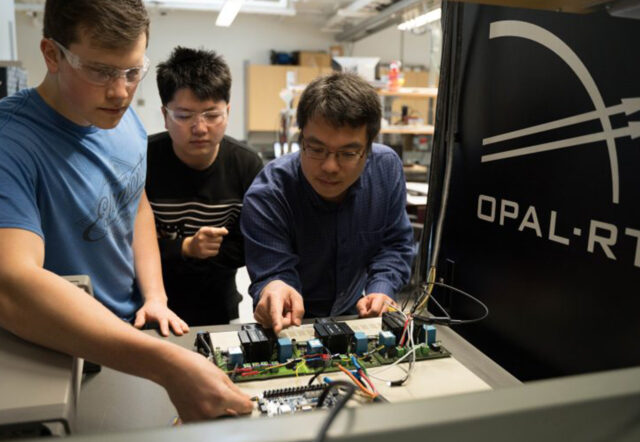
Academia and research
Enable cutting-edge education and innovation
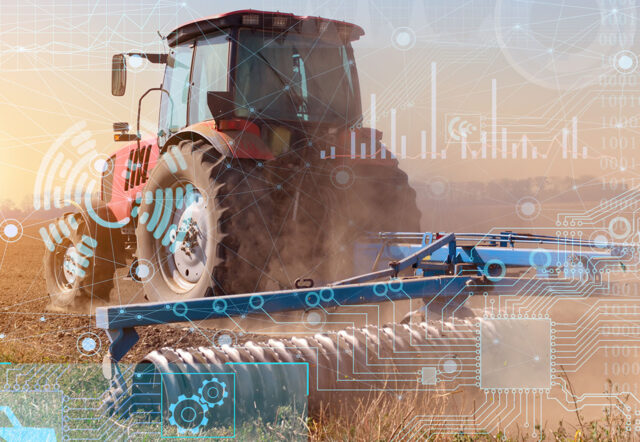
Autonomy
Accelerate the development of autonomous vehicles and robots with real-time sensor simulation and co-simulation tools
Partners
Best-in-class power amplification
We partner with global leaders in amplifier technology to ensure reliable, high-performance PHIL setups.
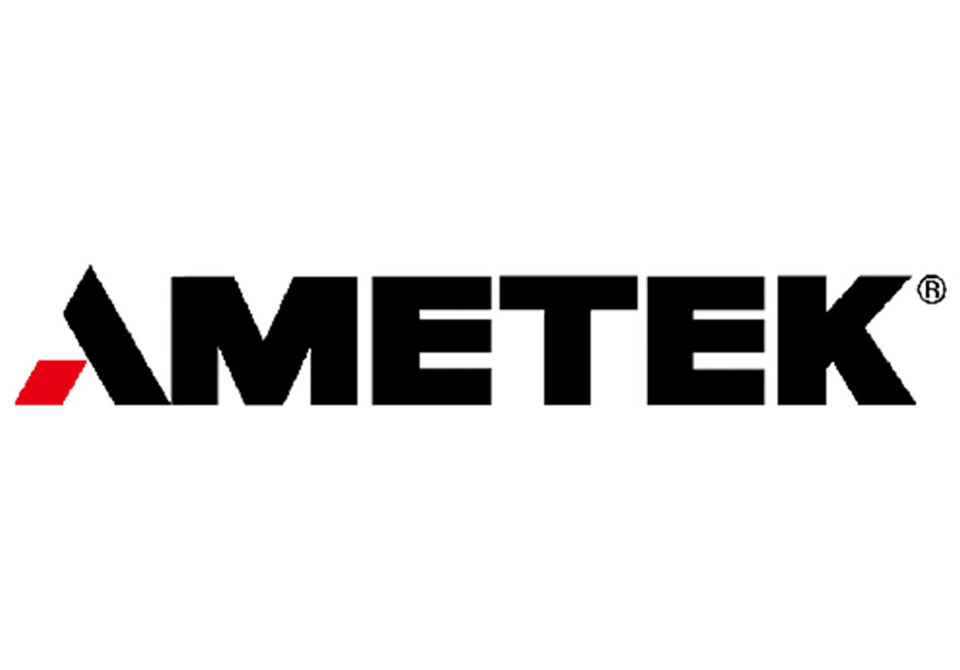
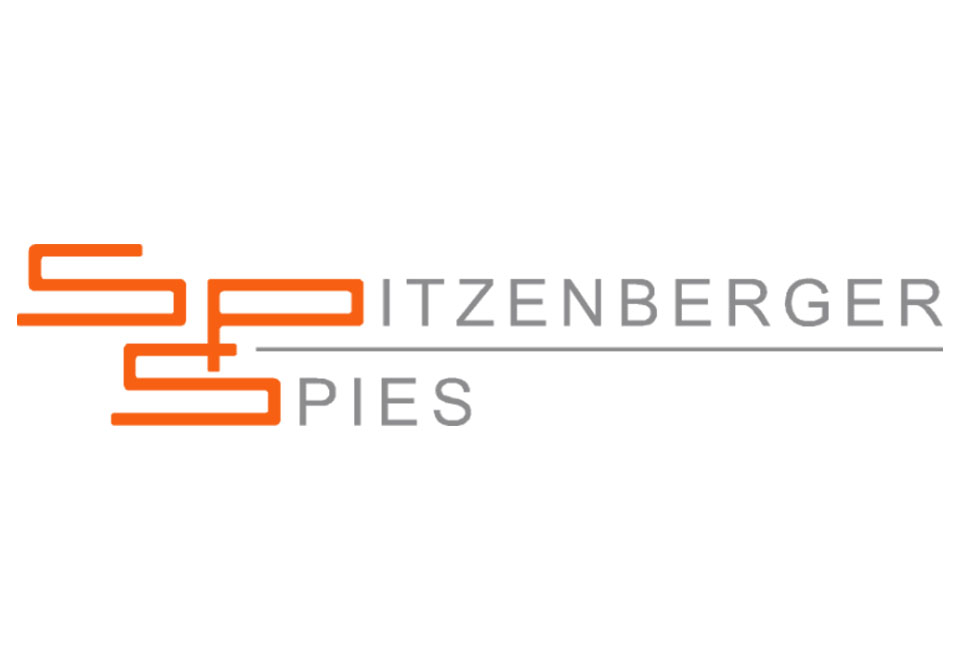
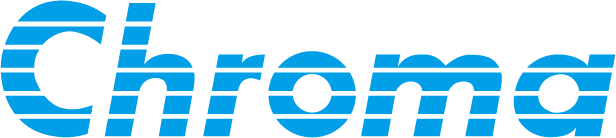
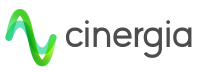
FAQ
Find the answers to your questions
What communication protocols do you support?
Consult our comprehensive list of supported protocols here: Communication Protocols.
What is power hardware-in-the-loop (PHIL) and how does it differ from traditional HIL?
Power hardware-in-the-loop (PHIL) builds on traditional hardware-in-the-loop (HIL) by enabling real power exchanges between our simulator and the physical device under test (DUT). Unlike conventional HIL, which only deals with low-level signal interactions, PHIL introduces a power amplifier to allow bi-directional energy flow, creating a closed-loop system that mimics real-world operating conditions more accurately.
Why is PHIL essential for testing power electronics systems?
We use power hardware-in-the-loop simulation to test power electronics with unmatched fidelity and safety. PHIL enables us to validate converters, inverters, and other power electronic devices under dynamic and realistic conditions—without needing full-scale physical test environments. This means we can simulate faults, load changes, and other scenarios while ensuring the DUT interacts with a realistic but controllable power system.
How does PHIL improve safety and reduce costs in power systems testing?
With power hardware-in-the-loop, we can replace complex and potentially dangerous physical test setups with high-fidelity real-time simulation. By using a power amplifier and simulator to replicate the grid or system environment, we eliminate many of the risks and costs associated with high-power hardware configurations—while still achieving accurate, real-world test results.
Can PHIL simulation help accelerate development cycles?
Absolutely. Our hardware-in-the-loop power electronics solutions using PHIL allow us to test early and often, even before full hardware prototypes are ready. Because we can simulate demanding operational conditions and see how real devices respond in real time, PHIL shortens iteration cycles, reduces debugging time, and helps bring products to market faster.
What types of systems and devices benefit most from power hardware-in-the-loop testing?
We apply PHIL across a wide range of applications including renewable energy systems, microgrids, motor drives, and EV powertrains. Any system involving power electronics—such as converters, generators, or BMS—can benefit from the realistic, closed-loop environment our power hardware-in-the-loop solutions provide.