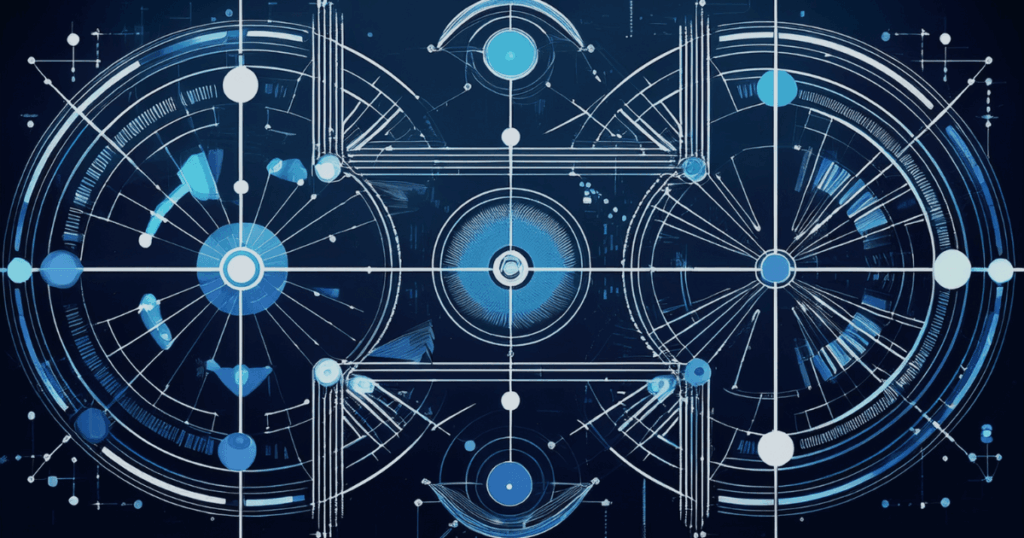
Efficient validation of control systems prevents costly setbacks and accelerates delivery schedules. Many development teams compare hardware in the loop vs software in the loop to refine their designs at every stage, from early concept to final deployment. Both approaches support comprehensive modeling of complex technologies, including embedded control systems, automotive powertrains, and aerospace instrumentation. A well-chosen strategy allows you to cut risk, optimize spending, and unlock greater returns on innovation.
What is hardware-in-the-loop?
Hardware-in-the-loop (HIL) involves connecting physical components to a real-time simulation platform to test control systems under conditions that closely match genuine operational scenarios. The simulator injects signals that replicate changing variables such as voltage, torque, or sensor inputs, allowing equipment like actuators or electronic control units (ECUs) to respond as if they were deployed in actual equipment. This method identifies potential design gaps early, preventing setbacks during final manufacturing steps. Engineers utilize HIL when precise interactions between real hardware and virtual models are vital for performance verification.
Physical prototypes come with substantial investment, so HIL methods provide assurance by confirming compatibility between actual devices and theoretical models before scaling up. Teams often select HIL when product safety and reliability must be validated at the subsystem or system level, especially in industries like automotive and aerospace. Consistent updates to physical components within a HIL environment also help unify stakeholder alignment, since each modification is tested against a digital replica. This approach ensures that crucial issues are revealed and corrected early, generating measurable cost savings and time-to-market gains.
What is software-in-the-loop?
Software-in-the-Loop (SIL) uses a simulated environment to execute and verify control algorithms or code without the need for physical hardware. Engineers embed the software within a virtual model that mimics the real control system, then feed it inputs representing various operating conditions. This setup reduces reliance on physical hardware at an early stage and uncovers software logic flaws or performance constraints more efficiently. Streamlined processes often result in faster feedback loops and shorter development cycles.
Many projects adopt SIL to address tasks like initial calibration, parameter tuning, or software-only regression tests. This approach translates to improved scalability, since development teams can spin up multiple simulations to evaluate different configurations. SIL supports better decision clarity because changes to the software do not require retooling or shipping out new hardware. These advantages help accelerate early development stages, improve cost-effectiveness, and set a stable foundation for advanced testing methods.
Types of HIL and SIL testing
Many teams rely on specialized HIL and SIL tests to verify control system quality at different project phases. Tests often vary in complexity, from basic module checks to complete system validations, ensuring that hardware or software performs reliably under diverse operating scenarios. A well-structured plan covers a series of test types tailored to unique project needs, resulting in faster feedback on both mechanical and software-related features.
- Single-component checks: Engineers test standalone algorithms or devices to confirm functionality under ideal or moderate operating conditions.
- Subsystem verification: Several components or subsystems are integrated into a combined testbed for a more holistic performance check.
- Stress and fault injection tests: The system or software is subjected to extreme or faulty inputs, verifying how it copes with worst-case conditions.
- Regression evaluations: Updates to software or firmware are validated against prior baselines, ensuring that newly introduced changes do not break existing features.
- Timing and synchronization assessments: Simulations confirm that real-time or near-real-time processes coordinate consistently, preventing latency-related issues.
- Algorithm validation: Control strategies and optimization routines are assessed for robustness when confronted with variable signals.
- End-to-end system trials: Complete solutions are tested to ensure that hardware and software integrate seamlessly before commercial release.
Comprehensive coverage of these testing types offers tangible advantages. Engineers obtain early insights into potential oversights, which reduces rework at advanced stages. A structured approach to HIL and SIL testing ensures consistent scaling, allowing critical components to be examined thoroughly. This effort also positions teams to take full advantage of advanced simulation platforms and relevant data analytics, paving the way for streamlined deployment across multiple industries.
Key differences between hardware-in-the-loop vs software-in-the-loop
The main difference between hardware in the loop vs software in the loop lies in the presence or absence of physical components during simulation. HIL incorporates real devices into the test bench, while SIL conducts experiments entirely within a digital environment. Both methods share a commitment to identifying faults early, but the hardware dimension in HIL provides deeper insights into physical interactions, such as timing, noise, or mechanical wear. SIL places stronger emphasis on rapid iteration of control software, saving time and resources before hardware is introduced.
A clearer view of these contrasts emerges through a concise comparison:
Aspect | HIL | SIL |
Physical components | Actual hardware integrated | Fully virtual testing |
Cost implications | Higher upfront investment | Lower hardware expenditure |
Testing focus | Combined hardware-software checks | Pure software verification |
Speed to modify | Limited by real equipment changes | Rapid software iterations |
Typical use cases | Automotive ECUs, aerospace sensors | Early-stage algorithm validation |
Organizations assessing software in the loop vs hardware in the loop often consider their end goals, budget constraints, and timeline before deciding. HIL is more effective at revealing hidden issues triggered by hardware responses, and SIL is better for quick refinements of control code. Balancing both techniques often provides the most comprehensive validation strategy, strengthening long-term reliability and accelerating market readiness.
Benefits of HIL and SIL in control system development
Many projects feature a blend of HIL and SIL strategies to reinforce reliability and efficiency. Combining these approaches provides robust coverage of both hardware-specific and software-centric elements, reducing risk and accelerating schedules. Teams discover that leveraging HIL and SIL together tends to improve product evolution, since each iteration can be validated quickly under realistic load scenarios. Full integration of these methods also enhances cost-effectiveness by pinpointing code or hardware issues early in the lifecycle.
- Faster time-to-market: Early detection of design flaws means fewer delays before commercial launches.
- Reduced risk: Potential failures or shortcomings are corrected in a controlled environment, limiting real-life liabilities.
- Improved resource allocation: Teams can decide when to invest in physical components based on insights gained during SIL.
- Scalability: Multiple versions of software or hardware modules can be tested quickly and in parallel.
- Enhanced quality assurance: Rigorous checks minimize uncertainties around reliability and performance.
- Simplified stakeholder alignment: Clear metrics from test outcomes help unify direction for managers and technical staff.
- Increased return on investment: The combined cost savings and faster progress boost long-term profitability.
Combining these benefits offers noticeable gains in product maturity and operational resilience. Effective HIL or SIL programs streamline processes for advanced projects in energy, aerospace, and many other fields, supporting breakthroughs that enrich growth. A well-managed approach to HIL vs SIL ensures that teams extract maximum value from high-fidelity simulation platforms and real components. That path fosters confident decision-making around new features or expansions in emerging markets, forming a better foundation for future enhancements.
Future outlook for HIL vs SIL simulation
Model complexity will continue to grow, reflecting the wider push toward interconnected embedded systems. HIL setups will probably incorporate more specialized devices that mimic real conditions, covering aspects like high-voltage energy storage or advanced sensor fusion. SIL frameworks will also expand into more powerful simulation environments, benefiting from AI-driven analytics that uncover software vulnerabilities at an earlier stage. These improvements aim to keep development teams flexible when introducing new features or optimizing existing algorithms.
Industrial applications in aerospace, energy, and transportation are expected to scale up their use of both sil vs hil testing methods. Integrating these simulations with cloud platforms helps streamline collaboration across global teams, cutting operational overhead and encouraging faster iterations. Such digital transformations favor businesses that demand short turnaround times and minimal rework. The result is likely to be an evolving testing ecosystem where physical prototypes, virtual models, and data analysis tools seamlessly share information for comprehensive verification.
A strong emphasis on safety and efficiency drives ongoing refinement in how hardware and software integrate. Large-scale expansions in battery management systems, autonomous transportation, and renewable energy networks count on advanced testing solutions that align hardware with robust software logic. That synergy grows more pivotal as market expectations push products to become more feature-rich and dependable. Engineers who adopt HIL vs SIL test processes early gain a clear advantage in innovation, risk reduction, and stakeholder satisfaction.
Real-time simulation strategies for control system advancement
Robust simulation across hardware and software domains stands at the center of modern product validation. An agile plan for adopting HIL vs sil ensures that emerging technologies are thoroughly tested before large-scale release. Wise resource planning focuses on using HIL for critical hardware-related risks and SIL for iterative code refinements, leading to a balanced approach that cuts costs and boosts reliability. Engineering teams that commit to comprehensive simulation programs produce solutions with greater confidence, often meeting regulatory demands and customer expectations more effectively.
Many organizations discover that a combined approach shortens design loops and enhances product flexibility. Upfront investment in real-time simulators can pay off rapidly when software modules are validated with minimal hardware exposure. That efficiency resonates across entire product lines, revealing fresh avenues for growth and profitability. A forward-thinking mindset built around HIL and SIL testing transforms standard engineering tasks into opportunities for accelerating time-to-value, strengthening stakeholder alignment, and ensuring seamless governance in high-stakes environments.
Engineers and innovators around the world are turning to real-time simulation to accelerate development, reduce risk, and push the boundaries of what’s possible. At OPAL-RT, we bring decades of expertise and a passion for innovation to deliver the most open, scalable, and high-performance simulation solutions in the industry. From Hardware-in-the-Loop testing to AI-enabled cloud simulation, our platforms empower you to design, test, and validate with confidence.