An engineer’s guide to inverter-based resources in power systems
Power Systems
06 / 04 / 2025
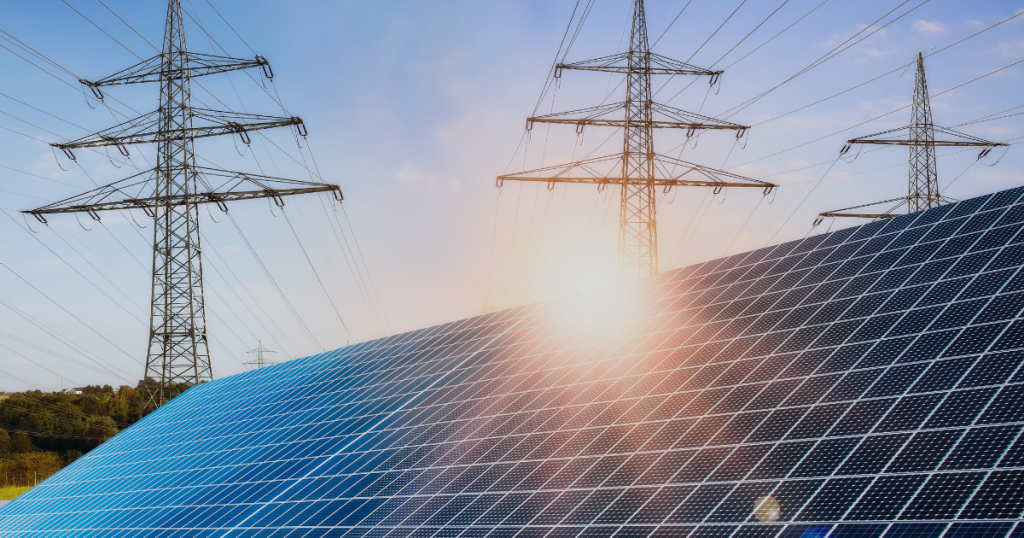
Picture a solar farm running smoothly even as clouds sweep by; that stability starts with an inverter-based resource you can trust.
What is an inverter-based resource and how does it function in power systems
An inverter-based resource (IBR) converts direct current (DC) into alternating current (AC) and injects that electricity into the grid under tightly controlled conditions. Because the conversion relies on power‑electronic switches rather than a spinning generator, an IBR can respond to grid events in milliseconds, shape its output waveform, and even absorb power when required. Every photovoltaic array, battery energy storage rack, and modern wind turbine contains at least one IBR.
Power electronics 101
An IBR starts with a semiconductor bridge, usually insulated‑gate bipolar transistors (IGBTs) or silicon‑carbide MOSFETs, that chops DC into a series of voltage pulses. A digital signal processor times the switching so those pulses approximate a sinusoid after filtering. Because no mechanical inertia exists, the device can modulate magnitude, phase, and frequency nearly instantly. That flexibility allows synthetic inertia, fast voltage support, and ride‑through functions that conventional machines struggle to match.
Control layers that matter
Every IBR ships with a multi‑layer controller. The inner loop regulates current to keep hardware within limits. The outer loop follows grid‑code set‑points such as active‑power reference, reactive‑power schedule, or frequency‑response profile. Supervisory software handles communication, fault diagnostics, and cybersecurity. When grid codes evolve, engineers can update firmware instead of overhauling hardware, an advantage that appeals to utilities watching standards tighten each year.
Grid‑side interaction
At the point of common coupling, the IBR measures grid voltage and frequency, then synchronizes its output using a phase‑locked loop. Harmonic filters smooth the waveform, while protection logic trips if voltage departs acceptable bands. Because IBRs lack synchronous inertia, they rely on advanced algorithms—such as virtual synchronous machine or grid‑forming modes—to help stabilize weak networks. Correct parameter tuning turns an IBR from a passive follower into an active grid supporter.
Why engineers are focused on inverter-based resources in modern grids
Utility‑scale renewables now account for a growing share of capacity, and almost all new plants interface through inverter‑based resources. Traditional synchronous generators are retiring, so grid planners need alternative voltage control, frequency regulation, and fault management. IBRs offer sub‑cycle response, firmware‑upgradable functions, and smaller footprints that fit inside dense urban substations. Their software‑defined nature lets asset owners roll out enhancements long after commissioning, which shortens project timelines and improves overall return on capital.
Types of inverter-based resources and where they are used in engineering
- Photovoltaic string inverter: Converts panel output to grid‑ready AC for residential and commercial rooftops.
- Central solar inverter: Aggregates multiple DC combiner boxes at utility‑scale plants for megawatt‑level output.
- Battery energy storage system converter: Manages bidirectional power flow for frequency support, peak shaving, and black‑start service.
- Type‑3 wind turbine converter (DFIG crowbar): Controls rotor currents to extract energy across variable wind speeds while meeting fault ride‑through requirements.
- Full‑converter wind turbine (Type‑4): Decouples generator speed from grid frequency, allowing maximum energy capture on large offshore platforms.
- Modular multilevel HVDC converter station: Moves bulk power over hundreds of miles with precise reactive‑power tuning at each terminal.
- Static synchronous compensator (STATCOM) within FACTS family: Provides dynamic voltage regulation in weak grids and industrial plants.
These represent more than just conversion hardware, they embody precision control and adaptability across a wide range of engineering needs. From residential rooftops to utility-scale renewable sites and high-voltage transmission corridors, each type supports critical functions like frequency control, reactive power support, and fault ride-through. Their versatility and scalability continue to make them a foundational component in modern grid design and validation workflows.
“Because no mechanical inertia exists, the device can modulate magnitude, phase, and frequency nearly instantly.”
The role of inverter-based resources in renewable integration and grid stability
Wind and solar output fluctuates with weather, yet frequency and voltage must stay inside tight limits. An inverter-based resource can dispatch fast frequency response within two to three cycles, hold voltage through reactive injection, and supply synthetic inertia by momentarily releasing stored energy from DC‑link capacitors or connected batteries. During faults, advanced grid‑forming modes ride through voltage dips, preventing cascading trips. As a result, transmission operators view IBRs not as a problem but as an asset for stability, provided their controls are tuned and validated.
Why simulation fidelity matters for testing inverter‑based resources in real time
A control‑level bug inside a 5 MW battery inverter can propagate across the grid far faster than human operators can react. Real‑time electromagnetic transient (EMT) simulation running the exact firmware lets engineers observe sub‑millisecond behavior under corner‑case faults. Lower‑fidelity tools may mask oscillations or misrepresent phase‑locked‑loop dynamics, giving a false sense of security. High‑fidelity hardware‑in‑the‑loop (HIL) setups capture pulse‑width modulation effects, device saturation, and communication latencies—insights essential when compliance fines or safety margins ride on every line of code.
Simulating inverter-based resources introduces several technical constraints that must be addressed early in the testing workflow. Intellectual property protection remains a top priority, as OEMs often require secure environments to share compiled control code without exposing source logic. Electromagnetic transient (EMT) models demand sub-microsecond resolution to accurately capture high-frequency switching behaviors, creating substantial computational loads in large-scale test scenarios. Control parameter variation across projects complicates modeling, requiring tuning flexibility without constant rebuilds. Additionally, evolving grid codes introduce new validation criteria that must be incorporated quickly to remain compliant. Reliable hardware interfaces are also essential—signal fidelity, I/O compatibility, and timing precision must align with field conditions to ensure testing results hold true at commissioning. Each of these factors directly impacts the reliability, scalability, and cost-efficiency of inverter-based resource validation.
Key challenges engineers face when simulating inverter-based resources
Simulating inverter-based resources introduces several technical constraints that must be addressed early in the testing workflow. Intellectual property protection remains a top priority, as OEMs often require secure environments to share compiled control code without exposing source logic. Electromagnetic transient (EMT) models demand sub-microsecond resolution to accurately capture high-frequency switching behaviors, creating substantial computational loads in large-scale test scenarios. Control parameter variation across projects complicates modeling, requiring tuning flexibility without constant rebuilds. Additionally, grid codes introduce new validation criteria that must be incorporated quickly to remain compliant. Reliable hardware interfaces are also essential—signal fidelity, I/O compatibility, and timing precision must align with field conditions to ensure testing results hold true at commissioning. Each of these factors directly impacts the reliability, scalability, and cost-efficiency of inverter-based resource validation.
“This shared confidence accelerates project approvals, shortens grid‑interconnection queues, and pushes innovation forward with quantified reliability.”
How OPAL‑RT supports testing and validation of inverter-based resources at scale
OPAL‑RT’s Blackbox Interface lets you load the genuine controller binaries supplied by the original manufacturer while keeping source code hidden from view, safeguarding intellectual property on all sides. The platform executes EMT models on multi‑core CPUs and FPGAs in the same chassis, so nanosecond‑accurate switching coexists with full‑network load‑flow studies. Built‑in APIs tie to MATLAB / Simulink, Python, and FMI, which means parameter sweeps or automation scripts fit straight into lab workflows. Utilities appreciate the ability to replicate site‑specific faults without extra hardware, while OEMs value the shorter certification cycles and smaller capital outlay. This shared confidence accelerates project approvals, shortens grid‑interconnection queues, and pushes innovation forward with quantified reliability.
Engineers and innovators around the globe rely on real‑time simulation to cut risk and unlock new value. OPAL‑RT brings decades of domain expertise plus open, scalable hardware‑in‑the‑loop solutions so you can design, test, and validate inverter-based resources with precision. From controller prototyping to cloud‑hosted batch studies, our platforms keep your projects on schedule and your stakeholders assured.