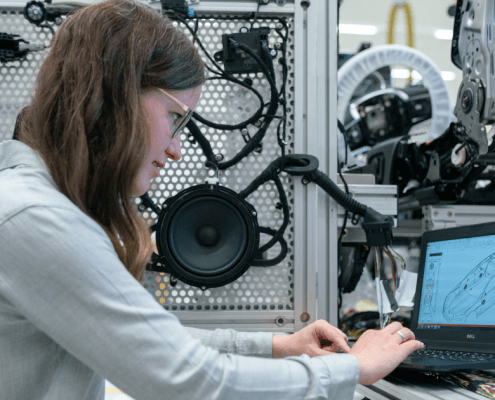
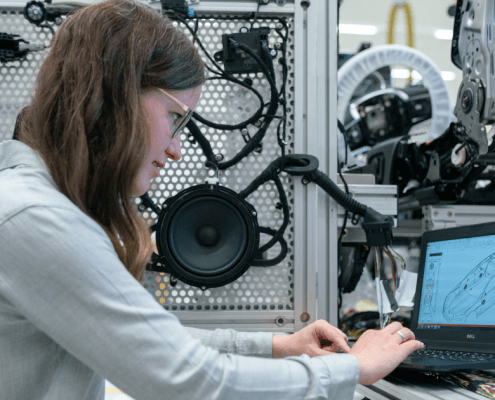
April 3, 2025
HIL testing in automotive delivers unmatched precision for validating critical control systems in modern vehicles.Â
Real-time simulation paired with accurate hardware emulation improves system reliability while reducing overall development costs. You gain a competitive edge in product design and testing through clear, measurable outcomes that accelerate time to value.
Engineers rely on these testing methods to verify system performance under realistic conditions, ensuring every component operates flawlessly before full-scale production. Testing strategies in automotive empower teams to fine-tune vehicle controls with confidence. The approach offers tangible results that enhance integration and streamline workflows. Your commitment to precision and efficiency is supported by real-time insights that drive smarter design choices.
Hardware-in-the-Loop (HIL) testing in automotive is a real-time simulation method used to validate embedded control systems such as electronic control units (ECUs), battery management systems (BMS), and advanced driver assistance systems (ADAS). In this setup, physical hardware is connected to a digital simulator that replicates the behavior of a vehicle and its environment. Engineers can test how the hardware responds to different driving scenarios, sensor inputs, and fault conditions without needing to use an actual vehicle.
This approach is essential for modern automotive development because it allows for early detection of issues, safer testing of edge cases, and faster iteration during the design process. HIL testing helps ensure that each component performs reliably under a wide range of conditions, improving system performance, safety, and compliance with industry standards.
“HIL testing in automotive provides a real-time simulation environment that replicates vehicle dynamics and control functions.”
A successful Hardware-in-the-Loop (HIL) testing setup in automotive applications depends on a well-integrated set of components that work together to bridge the gap between real hardware and simulated environments. These building blocks create a seamless interface for data exchange, enabling engineers to evaluate system performance with precision and consistency. Each component plays a distinct role, but it is their coordination that ensures the simulation behaves like a real-world scenario, maintaining the accuracy and reliability needed for rigorous testing.
Each part unites to form a complete simulation platform that accommodates a wide range of test scenarios. The result is a systematic approach to validate intricate functionalities with measurable outcomes. This structure fuels faster product rollouts, lowers operational costs, and boosts overall reliability. Teams gain a thorough view of system responses and can fine-tune control strategies in a controlled setting. These components offer a strong base for the next phase of development, reinforcing the importance of detailed testing.
Automotive development cycles carry significant costs and strict timelines that require meticulous planning. HIL testing in the automotive domain eases these pressures by offering a dependable and repeatable method to spot potential problems early. This approach supports better resource allocation and reduces the chance of high-impact failures. Confidence levels rise across teams when data is gathered in a structured, risk-free setting.Â
These gains lead to shorter release timelines and a more dependable quality standard. Teams experience fewer last-minute design overhauls, which streamlines the production pipeline. Additional refinements become possible when issues are captured in a simulated realm rather than on the assembly line. That type of agility fosters a development culture focused on incremental improvements and strategic growth. The result is timely deployment and consistent returns for stakeholders.
HIL testing in the automotive domain presents specific obstacles that call for targeted solutions. Preparation and methodical planning are crucial to getting the best performance out of test configurations. Teams must address everything from hardware compatibility to model fidelity if they want smooth execution. Lack of attention here can undermine the entire effort and inflate costs.Â
“Comprehensive HIL testing in the automotive domain stands as a vital tool for verifying autonomous driving systems.”
As modern vehicles become increasingly complex, Hardware-in-the-Loop (HIL) testing has emerged as an essential technique in the automotive development lifecycle. By simulating real-world conditions in a controlled, repeatable environment, HIL testing bridges the gap between software development and physical integration, allowing engineers to validate critical vehicle systems early and efficiently. This methodology plays a key role in reducing development time, minimizing risks, and ensuring compliance with performance and safety standards. The following sections explore how HIL testing is applied across various automotive domains—from powertrain and ADAS to electric vehicles and autonomous driving. Highlighting its transformative impact on innovation and system reliability.
HIL testing in the automotive domain provides critical insights into the performance of powertrain control systems. This section illustrates how real-time simulation is employed to replicate the dynamic behavior of engines, transmissions, and fuel management systems. Engineers observe how variations in load, speed, and environmental conditions impact the powertrain’s response, leading to refinements that optimize vehicle efficiency. The method confirms that each component functions reliably under diverse operational scenarios, ensuring that performance standards are consistently met and that system improvements translate into measurable benefits.
HIL testing supports the rigorous evaluation of advanced driver assistance systems by addressing the complexities inherent in sensor integration and algorithm validation. This simulation method enables engineers to assess sensor performance, braking response, and lane detection functionalities under varied conditions. The insights provided by HIL testing help optimize system configurations and improve passenger safety through enhanced feature reliability. Actionable feedback from this testing process leads to refined system responses and bolsters overall vehicle performance.
HIL testing is indispensable for validating electric and hybrid vehicle components. Simulation environments precisely replicate the behavior of battery management systems, inverter controls, and energy storage devices. Engineers gain detailed feedback on energy efficiency and system responsiveness, facilitating adjustments that improve overall vehicle performance. This approach not only reduces the need for costly physical prototypes but also supports rigorous testing of power electronics, ensuring that every component operates reliably under varied conditions.
Comprehensive HIL testing serves as a vital tool for verifying autonomous driving systems. This simulation method evaluates sensor accuracy, decision-making algorithms, and control responses by reproducing complex, real-world traffic scenarios. Engineers examine system behavior under unexpected events, enabling them to fine-tune algorithms and enhance vehicle safety. The outcome is a robust framework for autonomous driving that meets stringent performance standards and provides actionable insights for further system refinement.
Recent developments in automotive HIL testing have led to unprecedented levels of simulation fidelity and efficiency. The evolution of digital simulators and interface technologies continues to enhance testing capabilities, providing engineers with tools that offer real-time, high-precision insights into system performance. New hardware platforms, combined with advanced simulation software, support more detailed models that replicate every aspect of vehicle dynamics. These advancements result in shorter testing cycles and improved accuracy, making the overall validation process more effective.
Integration of AI-driven analytics and cloud-based simulation environments marks a significant advancement in automotive testing. These trends have redefined system validation by combining massive computational power with intelligent data analysis. Real-time monitoring and predictive analytics enable early detection of potential issues, reducing risk and optimizing performance. Continuous innovation in these areas solidifies HIL testing as an essential practice for modern automotive development.
Groups that invest in robust HIL configurations often discover fresh opportunities for scalability and cross-team synergy. The technique clarifies design criteria, explores complex interactions, and slashes the risk of unplanned rework. Additional assurance comes from testing multiple scenarios early, saving resources that would otherwise be spent on last-minute fixes. Executives, investors, and end users benefit from the resulting stability, leading to higher confidence across the board. HIL testing in the automotive domain stands as a practical strategy for delivering better vehicles in less time.
Automotive innovation demands speed, precision, and unwavering reliability and HIL testing is the catalyst driving it forward. At OPAL-RT, we deliver the high-performance simulation platforms engineers need to validate control systems with confidence. Whether you’re testing ECUs, BMS, or ADAS, our real-time solutions empower your teams to simulate complex scenarios, detect issues early, and accelerate vehicle development. Built for scalability and openness, our HIL systems are trusted by industry leaders shaping the future of mobility. Discover how OPAL-RT can help turn your vision of smarter, safer vehicles into reality, faster and more efficiently than ever before.
What defines HIL testing in automotive systems? HIL testing integrates real hardware with simulation software to replicate vehicle dynamics and validate control systems. It ensures that automotive components perform reliably under realistic conditions. How does HIL testing improve development cycles? This approach minimizes reliance on physical prototypes, enabling faster iteration and validation of design changes. The real-time insights provided contribute to shortened development cycles and cost-effective testing. What role does HIL testing play in safety validation? HIL testing rigorously examines safety-critical systems under simulated fault conditions. It offers a secure environment to verify that safety features meet the required performance standards. Why is real-time simulation important in automotive development? Real-time simulation delivers immediate feedback on system performance, crucial for addressing complex automotive challenges. It allows engineers to optimize control strategies and validate component interactions effectively. How does HIL testing support advanced automotive technologies? By replicating complex driving scenarios, HIL testing validates systems such as autonomous driving, ADAS, and electric vehicle components. It provides measurable insights that enhance design precision and operational reliability.