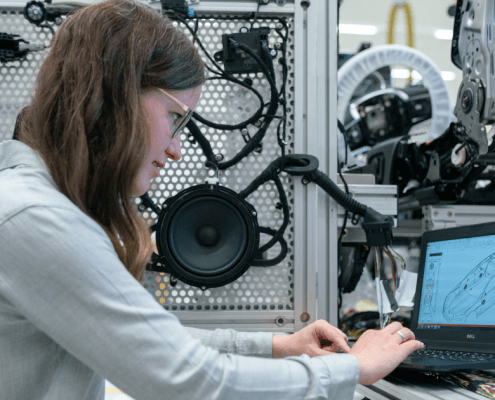
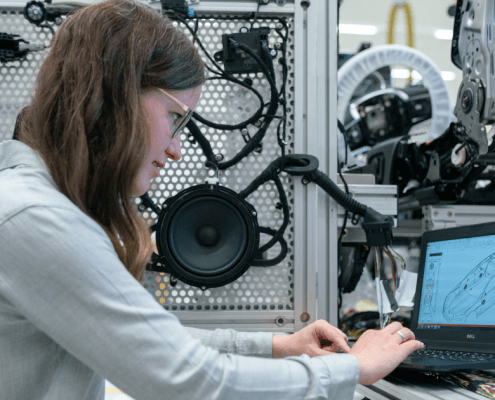
April 2, 2025
Hardware-in-the-loop testing is a direct method for predicting how physical equipment interacts with control software in real time. Engineers integrate actual hardware components with virtual models to fine-tune complex systems before large-scale manufacturing. This approach helps uncover design flaws early and avoids expensive rework. Project teams appreciate the precision and immediate feedback, which ultimately shorten development cycles.
Many engineering teams often ask what is hardware-in-the -oop and how it aligns with best practices for real-time simulation. HIL offers an advanced way to see how mechanical systems behave under varied operating conditions without constructing full-scale prototypes. Testing procedures become more streamlined and repeatable, helping you reduce cost. Integrating real sensors and actuators into a simulated test framework also ensures data accuracy for thorough analysis.
Hardware-in the-loop (HIL) testing often prompts a straightforward explanation: it links physical hardware components to a virtual model running in a real-time simulator. This setup evaluates genuine system performance under controlled conditions, which is essential when verifying safety, efficiency, or reliability metrics. Traditional bench testing might reveal certain issues, yet HIL offers deeper visibility because it replicates dynamic events in a repeatable way. Developers use this type of testing to confirm that control signals and power flows are properly managed before field deployment.
The approach typically involves connecting sensors, actuators, or even entire subassemblies to a digital domain designed to mirror operational scenarios. While software simulations alone can guide early development, the presence of tangible hardware adds a layer of authenticity that purely virtual methods cannot match. HIL helps you gather data on the physical responses to varying loads, temperatures, or voltage levels without building a costly test bench. Engineers across many industries, including power electronics and automotive, value HIL for accelerating validation schedules.
Control systems often exhibit complex interactions between multiple components, making them prone to hidden faults if tested only in simplified conditions. HIL provides a structured domain for testing every control loop with genuine hardware signals, thus capturing real performance data in real time. This reduces ambiguity and offers clarity on how sensors respond and how controllers adjust outputs based on the input conditions. Accurate insights gained from HIL allow engineering teams to refine algorithms and calibrate hardware interfaces more effectively.
For instance, a powertrain control system in an electric vehicle benefits from HIL testing by allowing the battery management unit, drivetrain components, and other modules to work together as they would in normal operation. This integrated approach leads to better alignment between hardware and software, minimizing unexpected failures after mass production begins. Large-scale projects see HIL as an integral strategy because it sets a high standard for performance evaluation at each phase. The result is a stable, well-coordinated system that meets or exceeds compliance requirements.
Organizations employ various HIL setups to match the specific demands of their development projects. Some solutions focus on micro-level component validation, while others handle entire assemblies or system-level interactions. Different configurations are chosen based on budget, testing frequency, or hardware availability. A well-planned HIL layout significantly boosts reliability and return on investment by ensuring that every part is evaluated under the right conditions.
Selecting the right configuration depends on the nature of your project and the extent of physical component integration required. Some teams combine multiple forms of HIL when working on large systems that span several domains, such as power distribution and vehicle control. Tailoring the approach ensures a balanced combination of scope and detail, yielding meaningful insights that drive better performance. Engineers who recognize these configurations can balance cost and testing depth, accelerating design cycles and production readiness.
Effective HIL implementation hinges on a methodical process that aligns real hardware and software models in a stable test domain. Each step addresses potential sources of error and ensures that you gather accurate data for advanced system tuning. Teams reduce cost overruns by mapping out a clear plan before integrating all components. The following core stages help you achieve consistency and thorough validation:
Clear objectives guide every successful HIL project. Engineers identify the control variables, performance constraints, and hardware specifications upfront. This approach helps you avoid confusion about the signals, data rates, and measurement ranges used during the tests. A structured list of requirements keeps the project focused and lowers the risk of scope creep.
Functional models of the system or subsystem are created in real-time simulation tools, ensuring that the virtual elements mirror the physical domain. Engineers calibrate these models based on known performance benchmarks, verifying that each parameter, such as voltage level or fluid pressure, reflects real-life values. Detailed modeling reduces guesswork in subsequent steps. Verification at this stage lays the groundwork for integrating hardware seamlessly.
Physical components such as sensors, actuators, or embedded controllers must connect smoothly to the simulator’s I/O channels. Proper cabling, signal conditioning, and data synchronization prevent faulty readings or missed events. This integration process often includes robust checklists to confirm accurate pin assignments and voltage references. Meticulous attention here guarantees that subsequent testing data remains trustworthy.
Initial trials confirm whether the combined hardware and simulation setup behaves as intended under controlled conditions. Engineers might run static load tests or simple operational scenarios to verify signal timing and data acquisition. These smaller evaluations help you fine-tune parameters before running high-fidelity scenarios. Addressing minor issues now can save significant effort once the system is fully operational.
Ongoing refinement is essential after the first validation cycle. Teams examine logs and performance metrics to make incremental improvements, focusing on control algorithms or hardware response times. This iterative approach enhances system reliability by catching subtle design issues early. Each refinement cycle moves the project closer to a validated, production-ready solution.
Implementing HIL may reveal complexities that require technical expertise, careful budgeting, or strong collaboration among multiple departments. These challenges can slow progress if not addressed systematically, yet foresight helps you reduce friction in the process. Some difficulties arise from hardware limitations, while others relate to organizational factors. Identifying these pitfalls early can substantially improve test outcomes.
Addressing each challenge often involves a blend of technology upgrades, process improvements, and stakeholder alignment. Even advanced teams can encounter setbacks when new components or updated specifications emerge unexpectedly. Practical contingency plans and a willingness to refine initial assumptions keep the program on course. Ultimately, resilience in handling these hurdles benefits the entire development lifecycle.
Project leads appreciate the consistent outcomes and measurable gains that HIL testing offers. Speed to market is often boosted by early detection of issues, and budgets are better managed due to fewer last-minute surprises. The flexibility of adding or substituting hardware components enables real-time diagnostics and iterative improvements. A closer look at these benefits highlights why HIL stands out as a practical approach.
Organizations that invest in HIL often view it as a strategic asset rather than an isolated testing tool. The capacity to link hardware and software under precise conditions fosters deeper learning about every subsystem. Collaboration around shared data speeds up decisions while ensuring compliance with industry standards. Over time, these benefits compound, resulting in more effective growth.
New developments in autonomous systems and renewable energy have placed HIL at the center of advanced product development. Engineers are integrating machine learning algorithms into the simulation loop, allowing predictive insights based on real sensor feedback. This shift elevates test coverage and helps you detect anomalies before they escalate into major failures. The growing need for zero-emission transport solutions also aligns with HIL to refine battery, motor, and charging systems at scale.
Cloud-based platforms now offer remote collaboration features, where distributed teams run large sets of HIL simulations concurrently. This technology accommodates broader test scenarios and speeds up your time to market. Enhanced synergy between hardware and AI-driven analytics refines control system calibration for better efficiency. Many companies view these HIL advancements as opportunities to tap into new revenue streams while minimizing overall risk.
Hardware-in-the-loop fosters robust system development across multiple sectors that demand high reliability and peak performance. The process connects real and virtual elements in a test bed that quickly flags potential issues and paves the way for cost-effective fixes. Engineers and project stakeholders rely on its accurate results to guide essential decisions for product deployment. When executed with a clear plan and scalable approach, HIL stands out as a key driver for quality and efficiency.
Engineers and innovators across industries are turning to real-time simulation to accelerate development, reduce risk, and push the boundaries of what’s possible. At OPAL-RT, we bring decades of expertise and a passion for innovation to deliver the most open, scalable, and high-performance simulation solutions in the industry. From Hardware-in-the-Loop testing to AI-based cloud simulation, our platforms allow you to design, test, and validate with confidence.
What does HIL stand for? HIL stands for Hardware-in-the-Loop. It is a technique that integrates physical hardware components into a simulated test framework to ensure accurate testing of complex systems. Is hardware-in-the-loop testing different from software-in-the-loop? Software-in-the-loop (SIL) testing focuses only on virtual models, while HIL adds actual hardware components for deeper insights. The presence of real hardware in HIL captures physical behavior and unique performance factors that SIL alone may overlook. How does HIL help reduce project costs? Budgets remain more stable because defects are discovered early, avoiding last-minute design revisions. Fewer prototypes and rework cycles also lead to substantial savings over the project’s timeline. Can HIL testing scale for high-voltage or industrial applications? Yes. Many platforms support higher power ratings, specialized I/O boards, and dedicated amplifiers to handle industrial demands while maintaining real-time performance. Why do teams ask what is hardware-in-the-loop testing in automotive? Engineers want a reliable way to verify electronic control units, powertrains, and safety functions before physical vehicle assembly. HIL exposes software and hardware to real sensor inputs, revealing potential issues under realistic conditions.