Product News
June 18, 2025
A Guide to BESS Battery System Testing for Power Engineers
A single millisecond of voltage sag can spell millions in lost revenue for a utility‑scale battery system.
Battery energy storage has stepped onto the main grid stage, and with that leap comes tighter rules, steeper financial stakes, and zero tolerance for unexpected downtime. You carry the responsibility of proving that every inverter firing angle, protection relay, and thermal loop will behave exactly as planned before a single watt is dispatched. The following guide explains why sub‑cycle validation is essential and how real‑time techniques give you hard evidence, not just pretty plots.
“Traditional off‑line studies fall short once you consider microsecond switching events, non‑linear battery impedance, and protection logic that must trip within four milliseconds.”
Why BESS Battery Energy Storage Systems Require Real‑Time Testing
BESS battery energy storage systems connect fast‑acting power electronics with electrochemical stacks that age, heat, and interact with a complex grid. Traditional off‑line studies fall short once you consider microsecond switching events, non‑linear battery impedance, and protection logic that must trip within four milliseconds. Real‑time testing reproduces these phenomena at full bandwidth, letting you watch the actual control code respond to synthetic grid faults, harmonic distortion, and cyber‑induced set‑point changes. Regulators now ask for this proof because spreadsheet averages cannot predict sub‑cycle chaos, and financiers favor hardware‑in‑the‑loop over costly field trials.
Key Parameters That Must Be Measured During BESS Testing
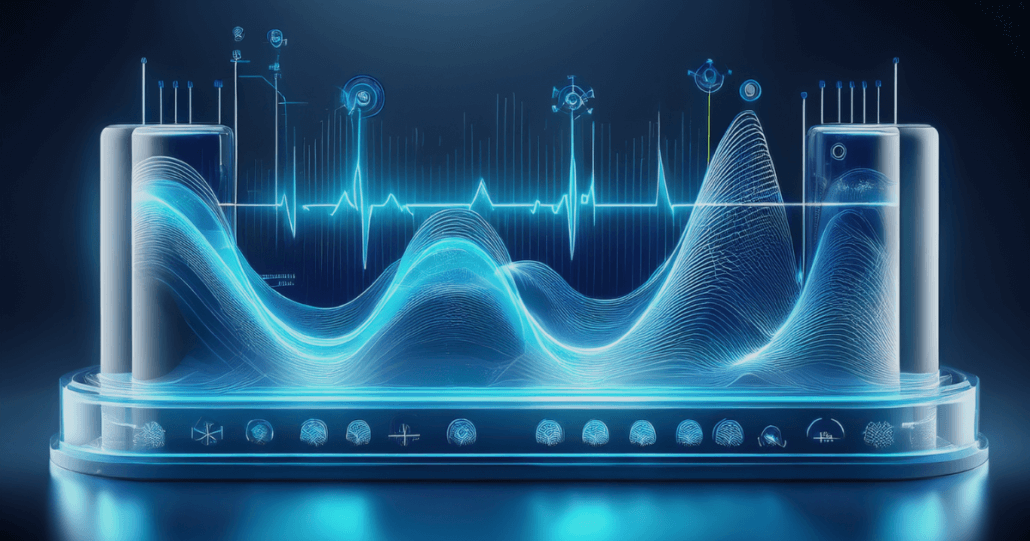
- State of charge tracking: Compare model prediction versus measured amp‑hour count at every time step.
- DC bus ripple: Quantify peak‑to‑peak variation to protect capacitor life and ride‑through margins.
- Per‑phase current imbalance: Spot deviations that hint at sensor drift or gating errors before contacts overheat.
- Converter switching losses: Measure real‑time efficiency to confirm thermal design headroom.
- Protection trip time: Record microsecond response to over‑current, over‑voltage, and sudden grid‑island events.
- Temperature gradient across cells: Correlate spatial heat maps with current draw to prevent runaway.
How to Test a BESS for Balance Accuracy and System Stability
Balanced State‑of‑Charge Calibration
The first step in how to test BESS for balance involves verifying that pack‑level algorithms apportion charge evenly across modules. Introduce asymmetrical load patterns in the simulator while monitoring individual cell voltages and currents. A well‑tuned balancer should damp the mismatch within a set window, often less than two percent state‑of‑charge deviation. Any sluggish response signals either sensor quantization or a control‑loop gain issue.
Dynamic State Estimation Under Grid Transients
Even a perfectly balanced pack can drift when the grid introduces a line‑to‑ground fault. Inject three‑phase faults, frequency swings, and harmonic bursts into the hardware‑in‑the‑loop bench. Observe whether the estimator maintains accurate internal resistance and open‑circuit voltage calculations under these harsh conditions. Stability here proves that your observer equations hold under the worst‑case noise levels.
Closed‑Loop Power Quality Validation
System stability goes beyond SOC balance; it reaches into active and reactive power regulation. Feed the inverter with rotating‑machine harmonics, variable‑speed wind ramps, and market‑driven power‑set‑point shifts. The goal is less than one percent total harmonic distortion at the point of common coupling, verified over a spectrum up to the 50th harmonic. Passing this test means the BESS battery system can meet power‑quality contracts without costly static filters.
Integrating Hardware in the Loop for Battery Energy Storage System Testing
Hardware‑in‑the‑loop (HIL) places the physical controller, protection devices, and communication links inside a closed loop with a digital plant running at microsecond time steps. For battery energy storage system testing, this method lets you examine unbalanced faults, cyber attacks on SCADA commands, or temperature excursions while the same control board slated for the field interacts under full duty cycle. Instead of constructing a one‑off power stage, you simply swap firmware versions or component tolerance files to study edge cases that would be unsafe on a live stack.
Real‑Time Simulation Tools That Improve BESS Test Confidence and Speed
High‑fidelity EMT solvers combined with field‑programmable gate arrays provide sub‑microsecond accuracy while keeping run times equal to wall‑clock time. When paired with automatic regression suites, these tools trim weeks off a test matrix: every nightly run can sweep hundreds of fault scenarios, compare pass/fail criteria, and deliver a concise report before the next workday. Multi‑rate co‑simulation links the detailed converter model with longer‑horizon thermal models so that short pulses still predict lifetime throughput. The result is fewer prototypes, faster root‑cause analysis, and audit trails strong enough for the strictest grid operator.
Avoiding Common Pitfalls When Testing a BESS Battery System in the Lab
- Skipping high‑frequency coupling: Omitting cable inductance yields unrealistically low ringing and hides gate‑drive weaknesses.
- Using ideal contactors: Perfect switching masks arc‑flash risks and underestimates wear cycles.
- Ignoring communication latency: Serial or Ethernet delays alter control stability but are easy to miss in pure software loops.
- Overlooking temperature soak time: Rushing tests without thermal equilibrium leads to misleading efficiency numbers.
- Treating firmware as frozen: Small version shifts change interrupt timing, so always retest after any code commit.
- Sharing grounds across unrelated subsystems: Unintended paths introduce measurement error and false trips.
“You can load the exact protective‑relay code supplied by an inverter OEM, connect the real PCB through standard fiber, and watch it drive a virtual grid fault—all without waiting for a physical prototype.”

How OPAL‑RT Supports Real‑Time Testing of BESS Battery Energy Storage Systems
OPAL‑RT equips engineers with open, modular simulators that run converter‑level EMT at 50 ns steps while hosting Python, MATLAB/Simulink, and FMI co‑models on the same clock. You can load the exact protective‑relay code supplied by an inverter OEM, connect the real PCB through standard fiber, and watch it drive a virtual grid fault—all without waiting for a physical prototype. Built‑in cybersecurity hooks introduce packet loss or spoofed commands so you can prove control resilience under NERC CIP compliance tests. Our engineering team acts as an extension of your lab, sharing playbooks for parallel‑processing tricks that finish a 200‑scenario validation suite before the weekend. When every hour offline carries a steep capacity‑payment penalty, that speed and clarity matter.
Energy storage now underpins renewable scheduling, frequency containment, and black‑start contracts. Real‑time testing brings the confidence needed to sign those service agreements with tighter margins and stricter penalties. Apply the methods covered here to move from assumption to proof and cut months off project timelines.
Engineers and innovators around the globe are shifting to real‑time simulation to cut risk and accelerate progress. At OPAL‑RT, we bring decades of domain expertise, an open architecture philosophy, and a passion for precision to every project. From hardware‑in‑the‑loop benches to cloud‑based batch runs, our platforms give you hard numbers you can trust when the grid operator calls.
Common Questions About BESS Testing for Power Engineers
What makes BESS battery energy storage systems harder to validate than conventional generators? Fast power‑electronics switching and electrochemical aging combine to create sub‑cycle dynamics that turbine‑based units rarely face. Real‑time HIL exposes these effects without putting hardware in jeopardy. Which standards guide BESS testing for grid interconnection? IEEE 1547‑2018, UL 9540A, and various utility grid‑code clauses outline fault‑ride‑through, power‑quality, and safety metrics that a BESS battery system must meet before commissioning. How does hardware‑in‑the‑loop shorten battery energy storage system testing schedules? The plant model runs at microsecond resolution, letting you apply hundreds of synthetic faults in hours, eliminate costly field trips, and reuse the same controller board for firmware iterations. Why is balance accuracy so important in BESS testing? Uneven state‑of‑charge across modules accelerates aging and can trigger protective shutdowns; balance verification catches these issues before contracts penalize underperformance. What performance metrics prove a successful BESS testing campaign? Typical sign‑offs include protection trip time under four milliseconds, harmonic distortion below one percent at the PCC, and verified model‑to‑hardware correlation within two percent across the load range.