Product News
June 25, 2025
Mastering Grid Forming vs Grid Following in Real-Time Testing
A power system only stays healthy if every inverter agrees on who leads and who follows, and that simple truth decides everything from voltage quality to blackout risk.
Why Grid Forming Inverter vs Grid Following Matters for System Stability
The main difference between grid-forming inverters and grid-following inverters is the source of their voltage reference; grid-forming devices create it, while grid-following devices wait for it. This single distinction drives stability. When an inverter establishes its own frequency and voltage, it can anchor weak grids, ride through faults, and share power with other sources even if the utility connection disappears. Grid following units, by contrast, synchronize to an existing waveform. They behave like precision current sources and withdraw as soon as that reference falters, so they cannot keep an islanded microgrid alive on their own.
Sudden disconnection events illustrate the stakes. If a wildfire isolates a feeder, grid-forming inverters hold frequency until crews close the breaker. If the same feeder relied only on grid-following units, all generation could trip, starving customers of power. At utility scale, a shrinking share of synchronous machines means fewer spinning masses to absorb shocks; grid forming control restores fast inertia electronically, smoothing frequency ramps and preventing protective trips. For engineers tasked with compliance under IEEE 2800 or meeting North American Electric Reliability Corporation (NERC) ride‑through profiles, choosing the right control mode is now a frontline design decision.
Key Differences Between Grid Forming and Grid Following Inverters
The main difference between grid-forming and grid-following topologies lies in the control strategy, but this choice cascades into hardware sizing, protection settings, and certification workflows. The comparison below highlights four areas engineers weigh during project planning.
Control Reference and Synchronization
Grid-forming inverters synthesize a voltage waveform internally, often with a virtual oscillator, and then push that reference onto the bus. Grid-following devices first measure the grid voltage via a phase‑locked loop, then inject current shaped to that reference. Because grid-forming units do not hunt for an external phase signal, they react in milliseconds when line conditions change, holding service in microgrids or on weak feeders. Grid following needs a stable grid to function, so it excels in strong transmission zones but yields authority when faults break that link.
Frequency and Voltage Support
A grid-forming inverter adjusts its frequency based on momentary power imbalance—mimicking the inertial response of a synchronous generator—while also drooping voltage with reactive power to share VAR duty across peers. This dual role supplies primary frequency regulation and voltage-var control without extra governors. Grid following units offer dynamic reactive support through adjustable power‑factor targets, but cannot police system frequency; their PLL will ride the drift instead of arresting it. That limitation pushes planners to add battery‑based flywheels or synchronous condensers if grid following dominates.
Fault Ride‑Through Behavior
Because grid-forming control loops track their own reference, they continue producing voltage during voltage sags, injecting the current needed by protection studies. The current magnitude is still limited by semiconductor ratings, yet the phase remains well‑behaved, reducing negative‑sequence stress on machines. Grid-following inverters experience PLL loss of lock during deep sags, so they may cease output precisely when the network requires support, triggering cascading trips. Advanced PLLs help, but they still trail grid-forming resilience.
Impact on Weak Grids
In feeders with high X/R ratios that shift resonances into critical frequency bands, grid-forming inverters suppress oscillations by establishing the dominant voltage source impedance. Conversely, grid-following inverters interact with this impedance and amplify voltage flicker, particularly when multiple units operate in parallel at a common coupling point.
“The main difference between grid-forming inverters and grid-following inverters is the source of their voltage reference; grid-forming devices create it, while grid following devices wait for it.”
When to Use Grid-Forming Inverters in Power System Design
Grid-forming inverters shine in any project aiming for self‑sufficiency or resilience. Remote mines, islanded military bases, and high‑renewable microgrids keep lights on during outages by assigning at least one inverter to form the grid. Hybrid plants that couple photovoltaic arrays with battery energy storage also lean on grid-forming control to deliver synthetic inertia and reserve headroom for frequency containment. Onshore wind farms connected through weak AC lines gain export headroom when the first turbines upgraded to grid-forming firmware stabilize voltage at the point of interconnection. Utilities commissioning HVDC links cite the same benefit: voltage‑sourced converters operating in grid-forming mode smooth power swings when DC faults clear.
How Grid Forming Supports Renewable Integration and Islanded Grids
Variable renewables introduce fast power ramps and low short-circuit currents, challenging legacy protection schemes. Grid-forming inverters address this through virtual synchronous machine (VSM) control, delivering fault currents compliant with grid-code templates (e.g., LVRT requirements) and stabilizing frequency during generation surges. In islanded grids, sudden load shifts (e.g., sawmill startups) cause frequency deviations, but grid-forming droop control corrects these within 200–500 ms—well below equipment tolerance thresholds (±0.5 Hz). Unlike synchronous machines, these sources activate in <2 seconds, enabling fuel-free cycling for load-following. Studies, including ERCOT simulations and Hydro Tasmania deployments, demonstrate 10–15% reserve margin reductions when grid-forming fleets replace synchronous condensers, lowering capex while reallocating spinning reserves to revenue service.
Common Challenges in Grid Forming Inverter Testing and Validation
- Model availability: Manufacturers guard proprietary firmware, so engineers lack detailed transfer‑function data.
- Controller‑hardware mismatch: Lab prototypes may run on digital signal processors, unlike the final field units, skewing timing.
- Network strength emulation: Replicating weak‑grid impedances at scale requires high‑bandwidth amplifiers or electromagnetic transient (EMT) solvers.
- Multi‑vendor coordination: Mixing grid forming and grid following suppliers complicates closed‑loop stability assessments.
- Compliance traceability: Demonstrating that real‑time testing matches IEEE 2800 waveforms demands synchronized measurement across controllers.
- Resource footprint: Full EMT simulation of a 300‑MW plant taxes CPU resources unless the platform splits tasks across FPGA and processor cores.
- Iterative firmware updates: Each patch alters control coefficients, requiring regression tests to lock trip settings before site roll‑out.
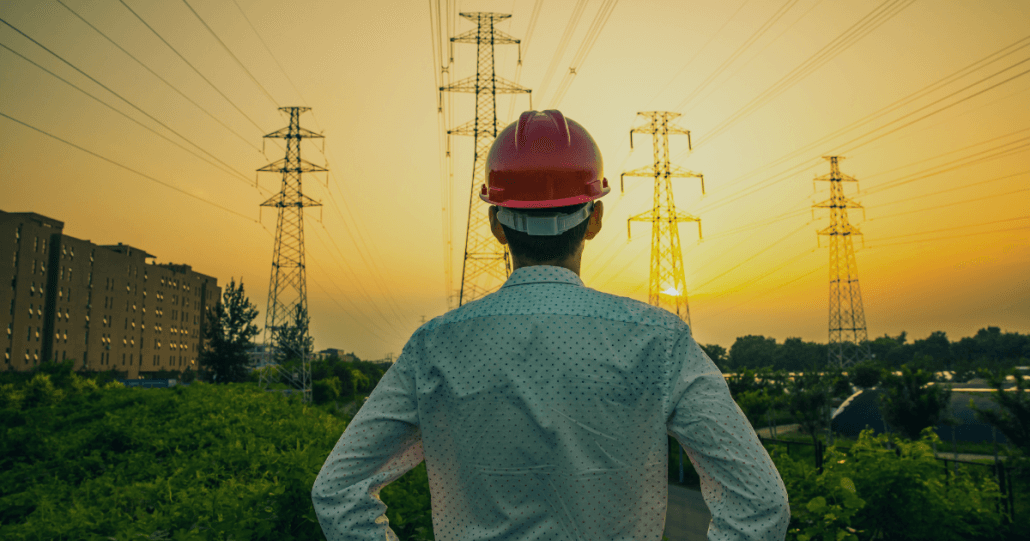
How OPAL‑RT Supports Grid Forming and Grid-Following Simulation
OPAL‑RT solves these testing pain points by letting you load the original equipment manufacturer’s control code into a protected Blackbox Interface that runs on FPGA‑CPU co‑simulation hardware. Intellectual property stays encrypted, yet you still probe inputs and observe outputs in real time, so grid-forming inverter vs grid following scenarios reach full EMT fidelity without extra cabinets. Multi‑rate solvers handle microsecond‑level switching alongside millisecond network transients, giving you sub‑100‑µs latency for hardware‑in‑the‑loop studies. Because the platform connects through standard protocols, you integrate SCADA, phasor measurement units, and protection relays on the same bench, trimming weeks from model‑validation cycles and cutting test‑lab overhead. Utilities, independent power producers, and OEMs rely on this open approach to vet grid forming compliance, shorten interconnection studies, and roll out firmware confident that field performance will match the bench.
Engineers and innovators around the globe are turning to real‑time simulation to accelerate development, reduce risk, and push the boundaries of what is possible. At OPAL‑RT, we bring decades of expertise and a passion for innovation to deliver the most open, scalable, and high‑performance simulation solutions in the industry. From hardware‑in‑the‑loop testing to AI‑ready cloud simulation, our platforms empower you to design, test, and validate with confidence.
“OPAL‑RT solves these testing pain points by letting you load the original equipment manufacturer’s control code—line for line—into a protected Blackbox Interface that runs on FPGA‑CPU co‑simulation hardware.”
Common Questions About Grid Forming vs Grid Following in Real-Time Testing
What is the main control difference in the grid-forming inverter vs grid-following debate? Grid forming units create their own voltage reference, acting as voltage sources, while grid following units synchronize to an existing reference and inject current accordingly. This control choice determines stability roles and protection settings. Do grid forming inverters cost more than grid-following units? Hardware prices are converging; the premium now lies mostly in firmware development and certification. As volumes rise, cost differences narrow, especially when avoided spinning‑reserve credits offset capital outlay. Can one plant mix grid-forming and grid-following inverters? Yes. Many hybrid projects assign a subset of inverters to grid-forming mode for stiffness while leaving the remainder in grid following mode for dispatch flexibility. Proper tuning and EMT testing prevent control interaction. How does grid-forming inverter testing differ from grid-following validation? Grid forming tests require weak‑grid impedance models, virtual inertial events, and islanding scenarios, while grid following tests focus on phase‑locked loop robustness and var support. Both still need fault ride‑through checks. Which standards cover grid forming performance today? IEEE 2800, IEC 60034‑32‑1, and emerging ENA guidelines address synthetic inertia, frequency‑watt response, and low‑inertia support. Many regional grid codes reference these documents for acceptance.